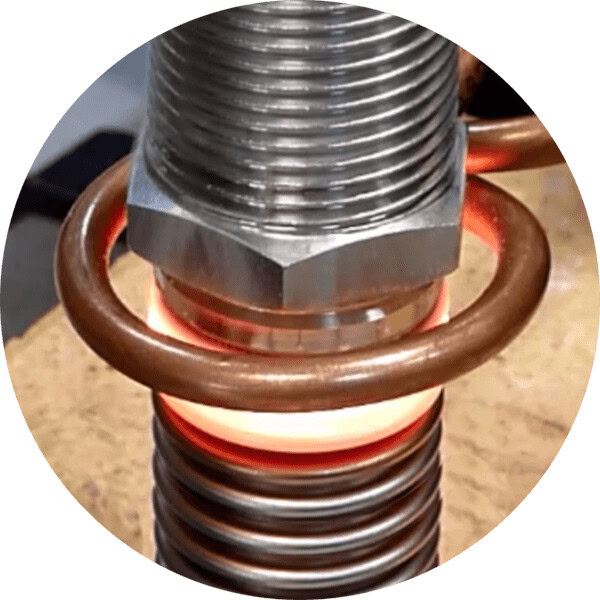
What is Induction Brazing?
Induction brazing is the process of joining two or more metals using induction heating. Induction heating utilizes the electromagnetic field to provide heat without contact or flame. Induction brazing is more localized, repeatable, and easier to automate compared to traditional torch brazing.
Induction brazing has been around for a long time but is only now coming into wider use due to advancements in induction heating power supplies.
The principle of induction brazing is similar to the transformer principle, where the inductor is the primary winding and the part to be heated acts as a single turn secondary winding.
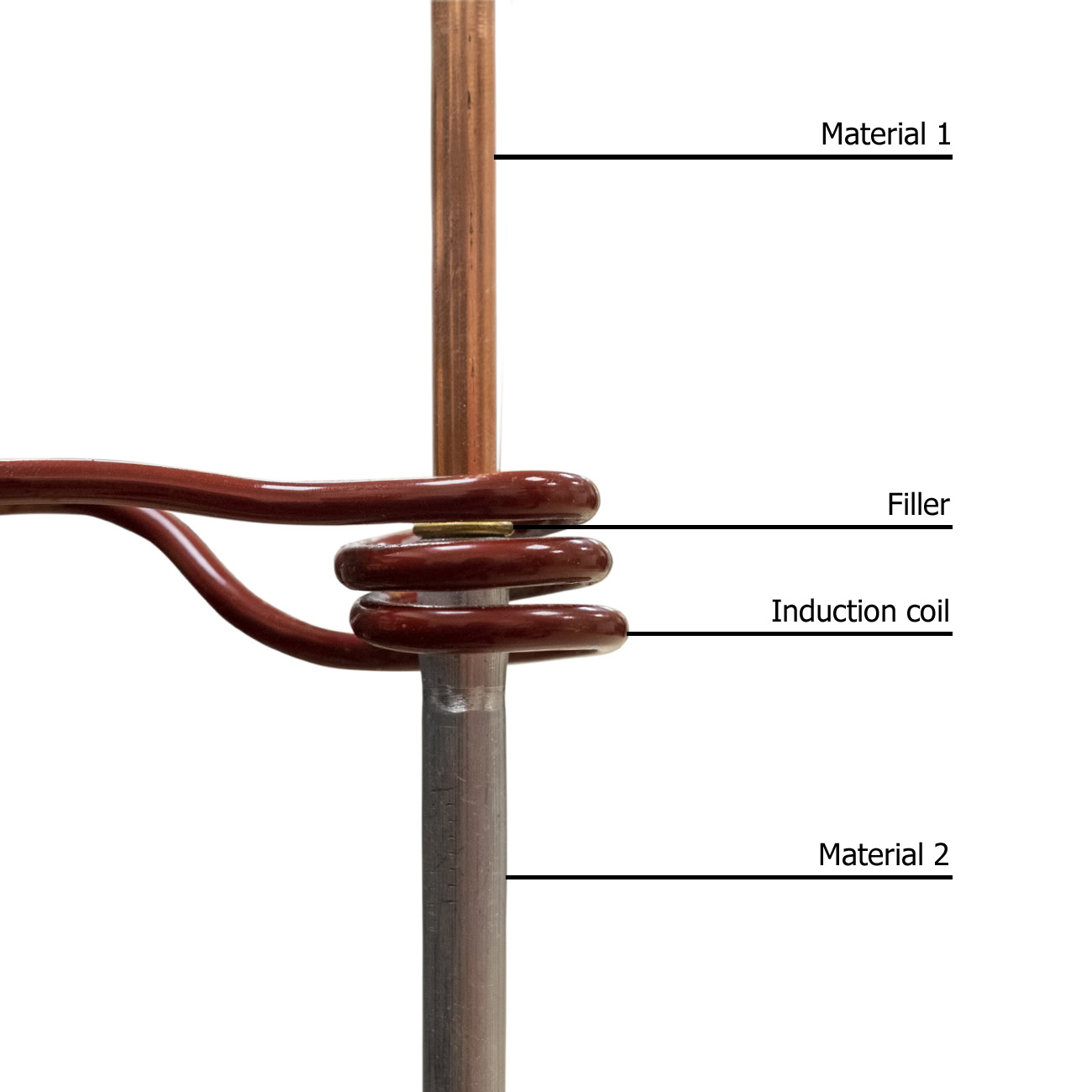
The main advantage of induction brazing is its precisely localized heat. The induction heating coil can be placed directly on the joint, providing a more consistent amount of heat than a torch. Another advantage is that induction brazing is more repeatable than traditional brazing. The induction brazing process has a predictable heat profile (essentially, the amount of heat provided over time), which is more consistent than traditional brazing and can be automated. It does not depend on operator’s skills as much as the torch brazing.
Induction brazing is a relatively new process, and it is not yet widely used. However, it is gaining popularity among manufacturers and is expected to continue to grow in the coming years.
Induction brazing can be used to join a wide variety of metals, including nickel, copper, cobalt, titanium, and steel. Some non-metals, such as ceramics, graphite and glass can also be brazed using induction. It is a great way to join dissimilar metals and alloys, thanks to its localized heat and ability to join metals without melting them. Because induction brazing uses electromagnetic field rather than flame, it can be used in many places where flame brazing is not possible or not safe.
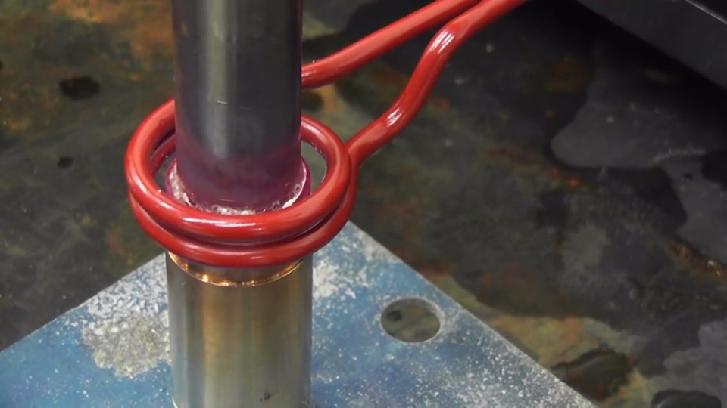
Induction brazing does have disadvantages. It is generally more expensive than traditional torch brazing. It may not be the best choice for complex, low volume parts and assemblies because it may require frequent change of heating coils. Induction brazing can be utilized in the most cost-effective way for high volume, repeatable processes, or relatively similar parts.
If you are interested in learning more about induction brazing, check out the resources below.