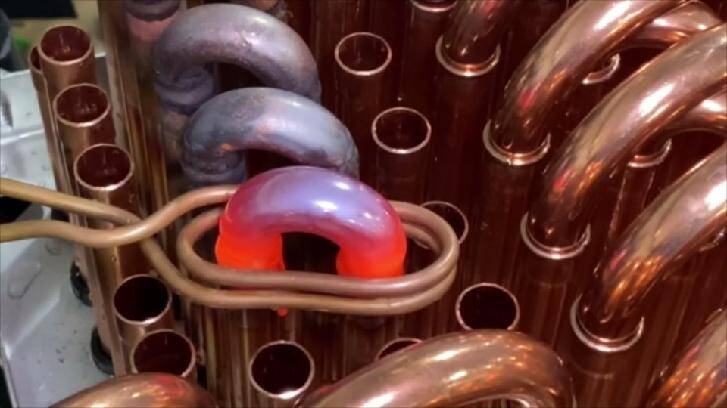
Torch brazing equipment has been the standard in heat exchanger production for many decades. However, it is not the most energy-efficient or cost-effective process.
This induction brazing test was conducted by our team for a leading manufacturer of heat exchanger equipment that is looking to replace torch brazing with induction heating to achieve precise control over the process, faster cycles, and improve energy efficiency.
Industry: Appliances & HVAC
Equipment:
UBraze hand-held brazing gun and an UltraHeat 15 kW induction heating power supply were used for this application. This induction brazing equipment ensures easy access to hard-to-reach areas and guarantees repeatability.
Process:
Our team was provided with a set of 120 copper tubes secured in an aluminum frame. All copper fittings are bent at 180 degrees. The fittings are connected with alloy rings. The main goal of this induction heating application is to braze the copper heat exchanger pipes in less than 20 seconds. A custom coil is designed to fit the dimensions of the pipes. Induction brazing is achieved at the power of 7.6 kW in 14 seconds.
Benefits:
The induction brazing gun ensures precise manual control over the process by focusing the heat to the desired area. The induction heating method is cleaner, safer, and requires minimum operator control compared to the torch brazing.
In addition, induction brazing is time-efficient and repeatable.
It allows the manufacturer to increase production rates, have fewer quality assurance issues and save on energy costs.
Reference Info: Application Note 3463-6663
To request more information about this Application test, please contact us.
Subscribe to our YouTube Channel
Video