SOLO Dragon 24 Induction Brazing Cobot
Dragon RoboStand 24 integrates the SOLO Series induction heating system with a Universal Robots cobot (UR 5, UR5e, UR10, UR10e) to achieve a fully automated brazing process. The induction heating system has been successfully used to replace the outdated and unsafe torch brazing widely used in the industry.
The integrated induction coil mounted directly onto the robotic arm is capable of reliably brazing multiple joints by applying controllable heat precisely positioned by the robotic arm.
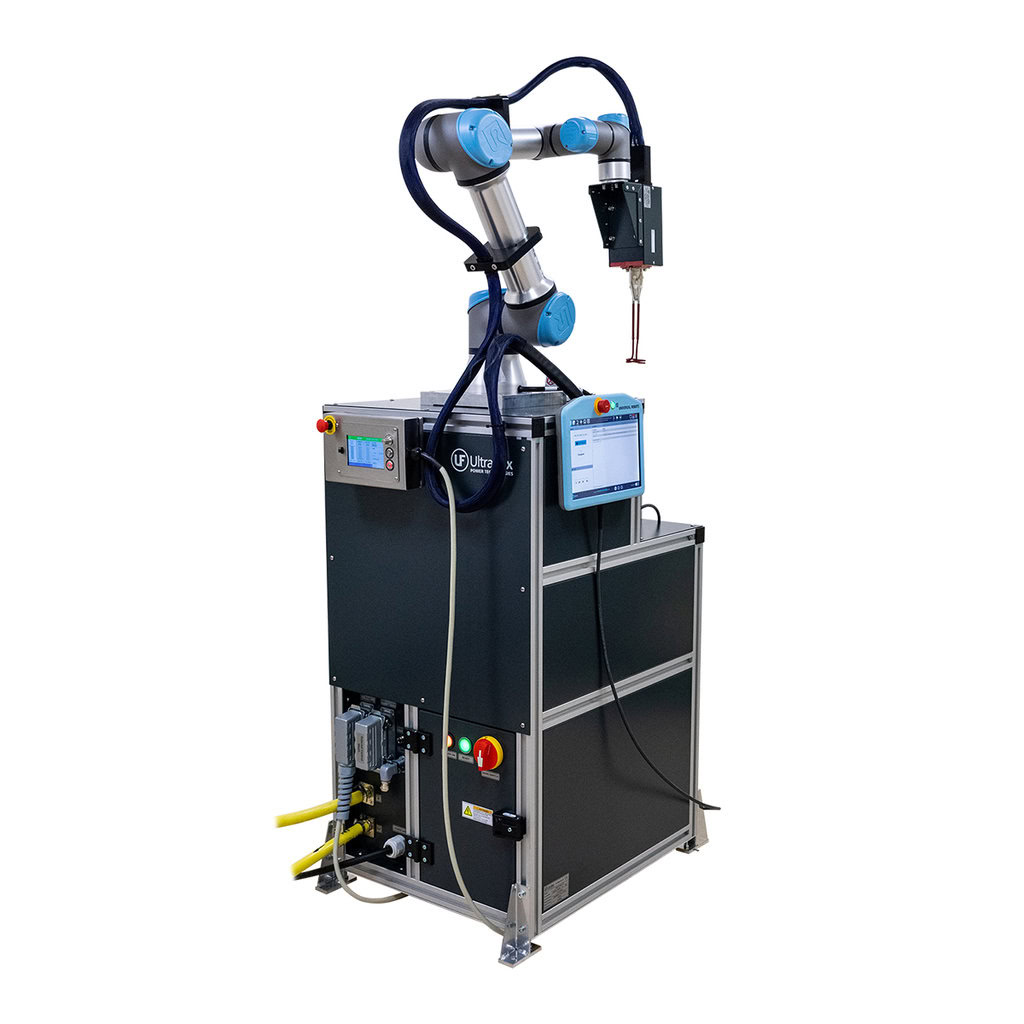
THE PROCESS
Dragon RoboStand 24 can automatically and consistently braze multiple joints located in predefined positions in an assembly. Brazing alloy rings are assembled onto the joints prior to the brazing process. The robotic system is pre-programmed to move to each joint and to apply power for a pre-programmed time to ensure a repeatable and reliable brazing process. An optional automatic wire feeding system can be supplied to feed the brazing alloy instead of using brazing rings.
The system can accommodate different production line speeds and multiple assemblies. It can be equipped with an optional vision system, capable of recognizing a variety of assemblies and positioning the brazing coil always at the correct joint location.
The Dragon RoboStand 24 is suitable for brazing copper-to-copper, copper-to-steel, brass-to-copper, and aluminum tubes. It is ideal for flameless brazing of refrigerator compressors, heat exchangers, home appliance components, and complex HVAC assemblies.
FEATURES
- High quality and repeatability of the brazed joints, achieved by precisely controlled positioning, coil power, and heat cycle
- Productivity from 3 to 10 Sec per joint achievable, based on the tube sizes and the type of brazing alloy
- Fully automatic process with no operator assistance required
- Programmable to braze multiple joints in complex assemblies
- Precise quality control is possible by monitoring the energy applied to braze each joint and comparing with reference value
- Flexible system, easily re-programmed to accommodate different process requirements
- Advanced 5” Color LCD touch control panel
- Digital I/O Interface – Remote Start/Stop or PLC Control
- RS485 (MODBUS) serial interface for remote computer monitoring, control, data logging and diagnostics
- Built-in temperature monitoring & control with K type thermocouple or IR Pyrometer (optional)
- Can be used with brazing rings (pre-forms) or integrated with automatic wire feeder to achieve fully automated brazing process
- Easy to integrate with a vision system
- Environmentally clean and safe process with no flames or toxic gasses