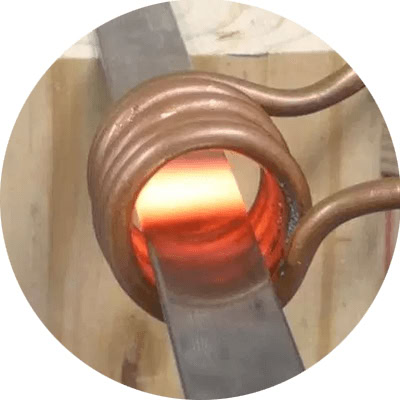
Understanding Induction Annealing
Induction Annealing is an advanced heat treatment process that involves heating materials above their recrystallization temperature. This method aims to achieve and maintain the desired temperature for a specific period, followed by controlled cooling. Widely used in metallurgy and materials science, induction annealing enhances the workability of materials by reducing hardness and increasing ductility, allowing them to undergo shape changes without breaking.
Advantages of Induction Heating in Annealing
Induction heating provides superior control over the annealing process. By precisely regulating the heating power, repeatable and accurate heating profiles can be easily achieved. Unlike conventional methods, induction heating directly heats the workpiece using a magnetic field, resulting in a faster and more responsive process. Additionally, the high efficiency of induction heating is particularly beneficial for lengthy treatments, reducing energy consumption and operational costs.
Benefits of Induction Annealing
Compared to traditional annealing methods, induction annealing offers several significant advantages:
- Precision and Control: The ability to fine-tune the heating process ensures consistent and uniform treatment of materials.
- Speed and Efficiency: Direct heating via a magnetic field allows for quicker response times and reduced processing durations.
- Clean and Contactless Process: Induction annealing is a non-contact method, which means it is cleaner and easier to automate, leading to higher-quality finished products.
- Versatility: This method is suitable for a wide range of materials, from ferrous metals to non-ferrous metals like copper and silver.
Applications of Induction Annealing
Induction annealing is used in various industries, including automotive, aerospace, and manufacturing, to improve the mechanical properties of components. It is ideal for processes that require precise temperature control and consistency, such as:
- Annealing of steel wires and tubes: Enhancing ductility and reducing brittleness.
- Heat treatment of copper and aluminum components: Achieving desired mechanical properties for electrical and thermal applications.
- Preparation of metal parts for further processing: Ensuring optimal performance during machining, welding, or forming.