Carbide Tipping with Induction Heating
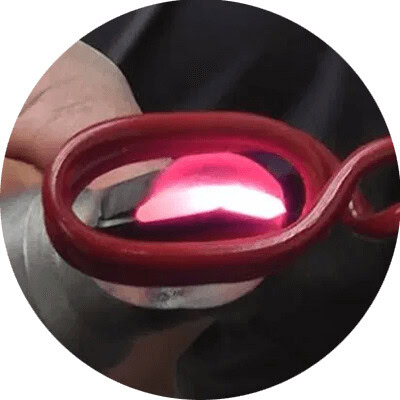
UltraFlex Power Technologies offers precision induction heating solutions for carbide tipping applications. Our systems ensure superior brazing quality, energy efficiency, and automation-ready capabilities. Discover how induction heating enhances tool performance and production throughput.
What is Carbide Tipping
Carbide tipping is a specialized brazing process that joins extremely hard, wear-resistant materials—typically tungsten carbide—with tougher and more ductile base metals such as steel or iron. This technique is widely used in the manufacturing of cutting and drilling tools, where the carbide tips endure intense friction and mechanical wear during operation. By brazing these durable carbide inserts onto the reusable metal body, manufacturers can extend the lifespan of the tools significantly. Once the carbide tips are worn out, they can be replaced without needing to discard the entire tool, making the process both cost-effective and resource-efficient.
Common Base Materials for Carbide Tipping
Different base materials require specific considerations when bonding with carbide inserts. Induction heating ensures precise, localized heat delivery, minimizing the risk of material degradation and improving joint quality. Understanding the properties of each base material helps optimize the carbide tipping process and extends tool performance under harsh operating conditions.
Base Material | Typical Use | Considerations |
---|---|---|
Tool Steels (e.g., High-Carbon, HSS) | Carbide-tipped saw teeth, drills, lathe tooling | High hardness requires localized heat; induction limits heat-affected zones and preserves temper. |
Alloy Steels (e.g., 4140, 4340) | Mining cutter heads, milling bodies | Toughness supports brazing temperatures. Thermal expansion differences managed with quick, localized heating and sometimes tri-metal braze foils. |
Stainless Steels (e.g., 304, 410) | Wear sleeves, surgical tools, shafts | Requires vigorous flux or inert atmosphere to avoid oxide formation; precise temperature control prevents overheating. |
Cast Iron (Gray, Ductile) | Engine parts, cast tool bodies | Controlled heating and slow cooling prevent quenching stresses and cracking risks. |
Advantages of Induction Heating for Carbide Tipping
Induction heating provides manufacturers with a fast, efficient, and precise method for carbide tipping operations. Compared to traditional brazing methods, induction minimizes thermal distortion, reduces energy consumption, and delivers consistent, repeatable results—making it ideal for both manual processes and full automation.