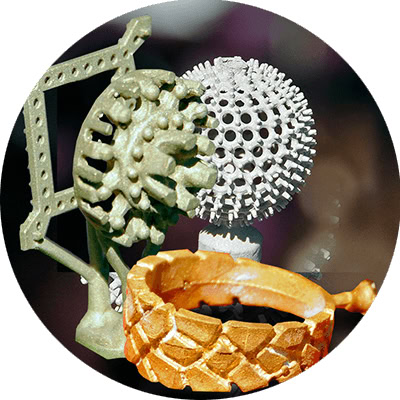
What is Induction Casting?
Induction casting is a process for one-step creation of either complex or simple designs from melting materials. It involves melting and heating to a suitable temperature after which the liquid material is poured into a proper mold or cavity to keep its shape during solidification.
Casting is often implemented for manufacturing of different parts and tools. Various materials can be used for molds – either expendable or long-lasting. To prevent the sample from contamination during the induction casting process, vacuum or protective inert gas (usually argon) is often applied.
Induction heating provides several important benefits for the casting applications. It is a contactless approach, which protects the samples from contamination and allows precise temperature control preventing overheating and premature solidification of the material.
When metal mixtures undergo induction casting, the high-frequency magnetic field helps for the homogenization of the resultant alloy. As a result, high quality and increased repeatability of the process can easily be obtained without the need to stir the mixture during heat-up.
Induction heating is suitable for all the different types of metal casting processes – centrifugal casting, continuous casting or die (high-pressure) casting.