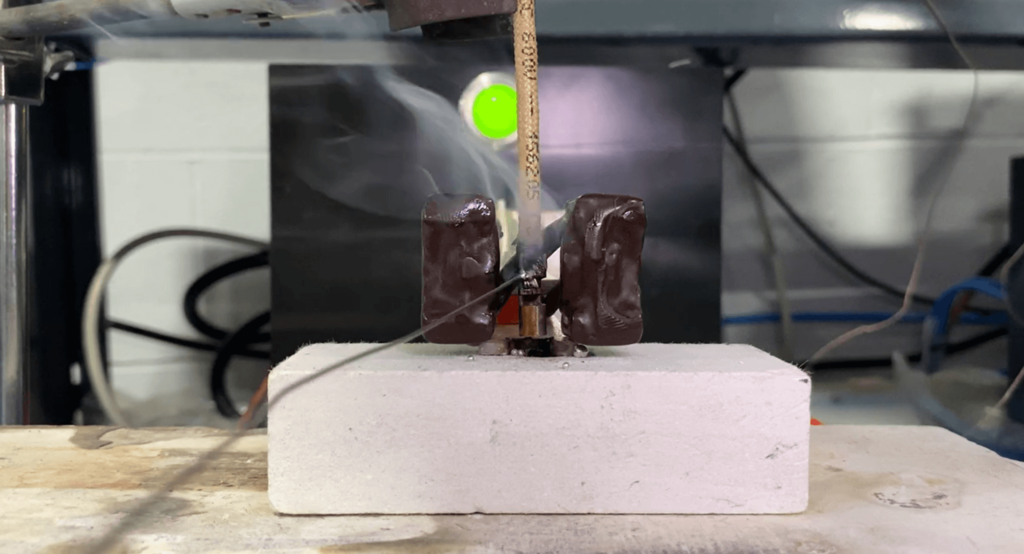
Objective:
A semiconductor company is considering replacing flame soldering with induction soldering to flow solder into voids of a crimped joint part of an AC wire cable. Induction heating will improve the electrical contact, thus optimizing the current manufacturing process and improving reliability, repeatability, and precision.
Industry: Electrical Components
Equipment: UltraFlex recommends the UltraHeat S 2 kW induction heating system which is commonly used in induction soldering applications.
Process:
A key process requirement is to use a high-temperature solder that can withstand up to 400-500 °C (752°F – 932°F). Flux is applied to clean the surface oxides on the crimp joint and to allow the solder to stick to both the copper wires and the connector. The solder wire can be manually fed, or the process can be automated with the use of pre-form solder rings crimped into the joint, or through a wire feeder. Induction soldering was performed with an open-end soldering coil. The induction soldering process achieved the soldering temperature requirements in 5 seconds.
Benefits:
Using induction heating for the soldering of AC wire allows the process to be fast, repeatable, reliable, and efficient.
Read more about other induction soldering applications.
To request more information about this particular Application test, please contact us.
Reference Info: Application Note 3463-6774
Subscribe to our YouTube Channel:
Videos