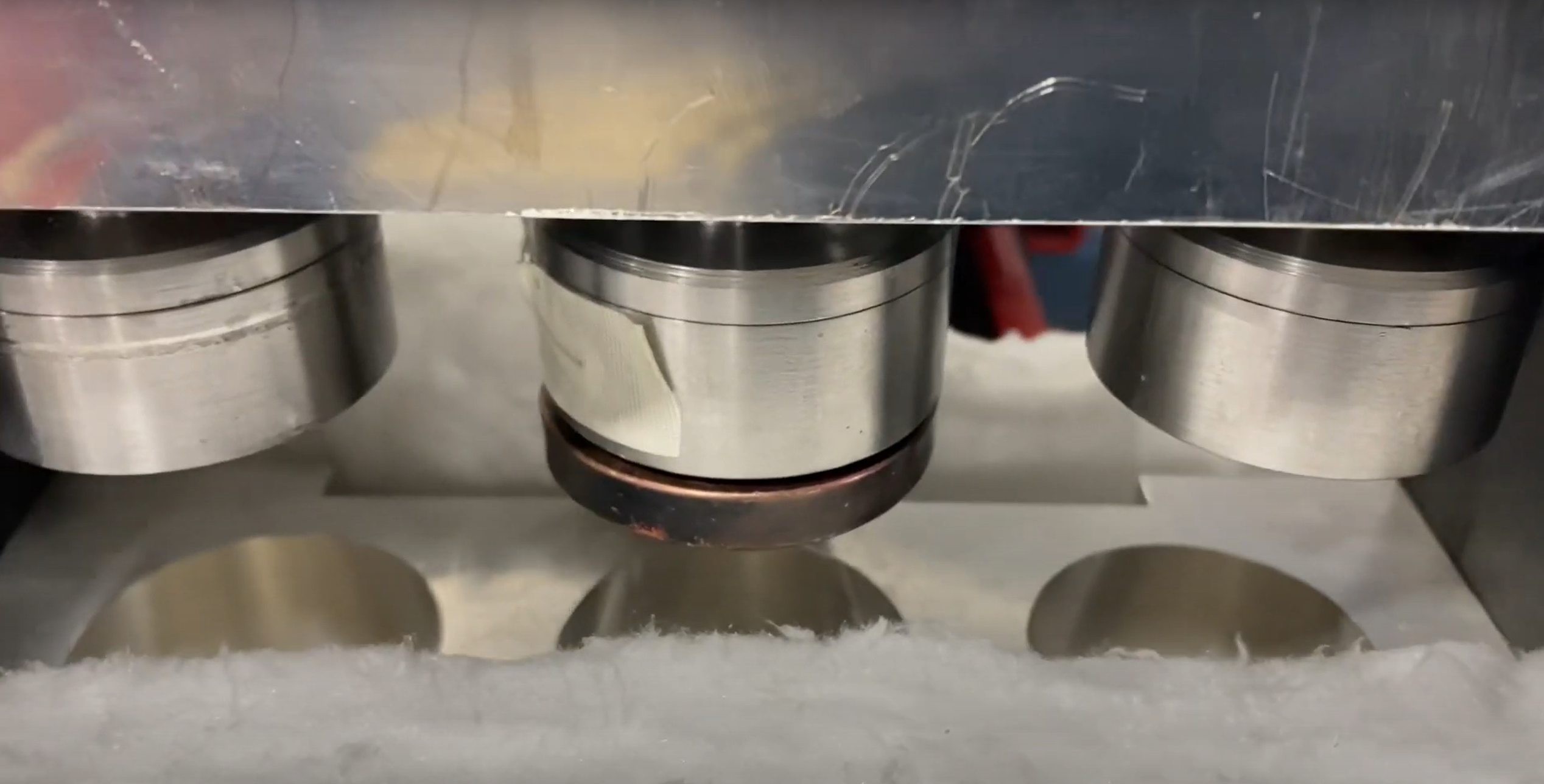
Objective:
In the world of manufacturing, precision and efficiency are paramount. Here is an example that goes to show that. A customer in the manufacturing industry needed to develop a cutting-edge process and automation technology to determine the reheating duration of a piston after insertion into a cylinder for 4 minutes. As a technological leader in energy efficiency and process improvement UltraFlex Power Technology was challenged to set up and validate this process. Embracing the task, we started with evaluation and preliminary simulations of the job. Two components should be preheated to 230°F. Additionally, the aim was to assess the time required to heat the part to 230°F from room temperature and if feasible, to reduce this time to a level of best ratio productivity/quality
Industry: Manufacturing
Equipment Used:
- Power Supply: SMT5, detuned to SMT2 specifications
- Heat Station: HS4W
- Thermocouple: K Type
Materials:
Magnetic Steel Pistons (2.25" outer diameter x 1.25" height
Key Parameters:
Fixed heating temperature: 230°F (110°C)
Process Overview:
In order to reach the goals laid out by the customer, we conducted four rigorous tests to evaluate the heating process. Our mission was to determine the time required to heat the pistons from room temperature to 230°F and then reheat them after a four-minute retraction period.
Test Details:
Test 1:
In the first test, we focused on heating the piston samples using the SMT5 power supply, which was detuned to SMT2 specifications. The heat station model HS4W was employed to achieve the desired temperature range of 95 to 230°F. The heating cycle time was approximately 40 seconds, with temperature control ensuring precision. The power output reached a maximum of 2013 watts, operating at a frequency of 125 kHz.
Test 2:
The second test aimed to optimize the heating process further. We continued using the SMT5 power supply, detuned to SMT2 specifications, and the HS4W heat station. This time, the temperature range was narrowed to 198 to 230°F, and the heating cycle time was reduced to around 26 seconds, again with temperature control. The power output was adjusted to a maximum of 630 watts, with a frequency of 124 kHz.
Test 3:
In the third test, we explored the effects of a timed heating cycle. Using the same SMT5 power supply and HS4W heat station, we maintained the temperature range of 198 to 230°F. The heating cycle time was further reduced to approximately 14 seconds, with a timed cycle replacing temperature control. The power output reached a maximum of 2002 watts, operating at a frequency of 125 kHz.
Test 4:
The final test involved heating a stainless-steel piston with a 2-inch outer diameter and 1 1/8-inch height. For this test, we used the SMT5 power supply and the HS4W heat station. The temperature range was set between 200 and 230°F, and the heating cycle time was significantly reduced to around 5 seconds, utilizing a timed cycle. The power output was increased to 5 kW, with a frequency of 139 kHz.
Additional Insights :
Our journey revealed that an SMT 2/200 power supply is sufficient for reheating the piston to the required temperature. However, due to the customer's requirement for longer bus work, we utilized a higher power supply (SMT5 with 3ft flex leads) in Test 4. An oblong pancake coil approximately 3.5 inches long was identified as optimal for supplying sufficient heat as the part passes over it.
Reference:
AR 3463 – 7431
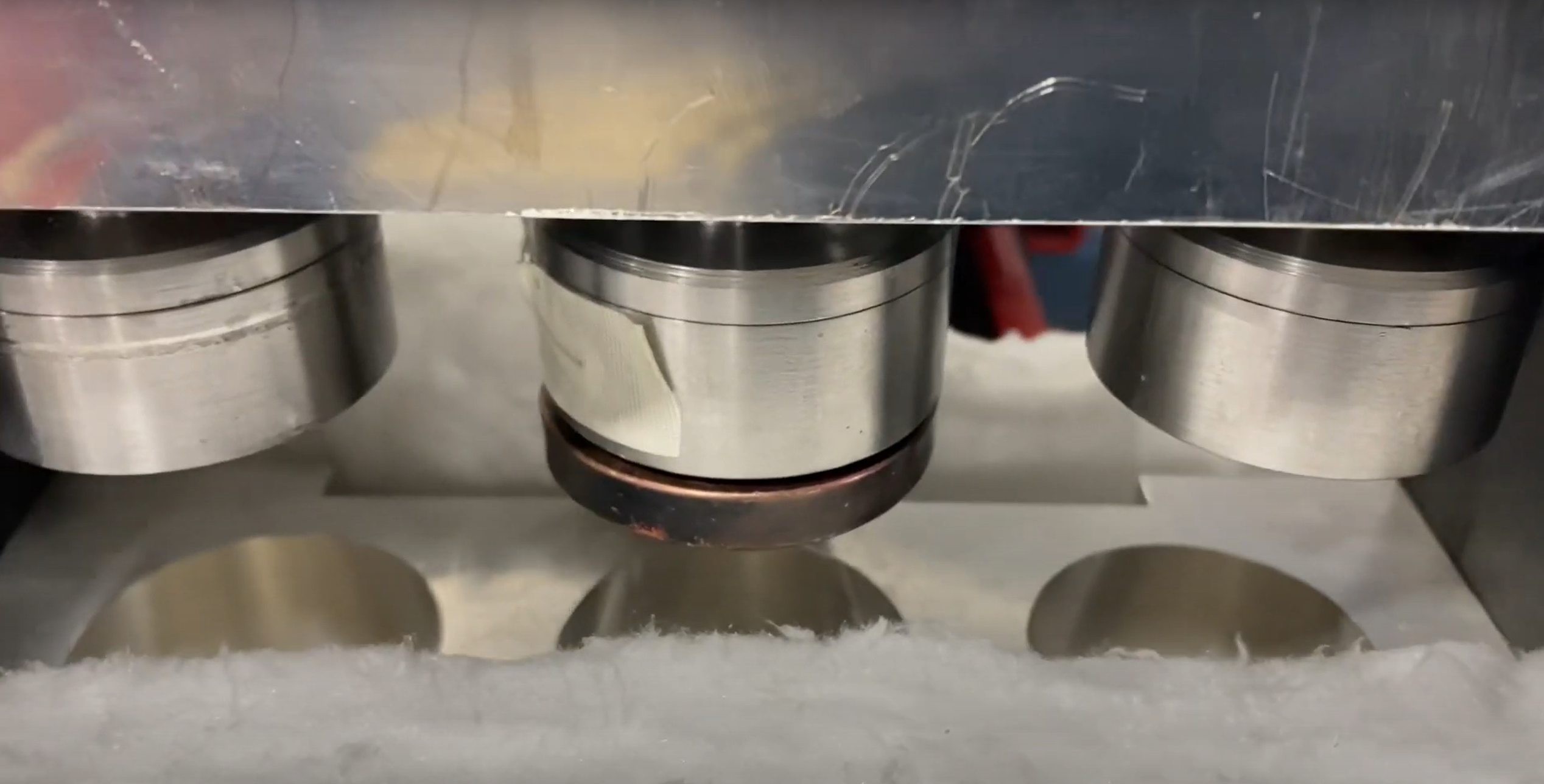
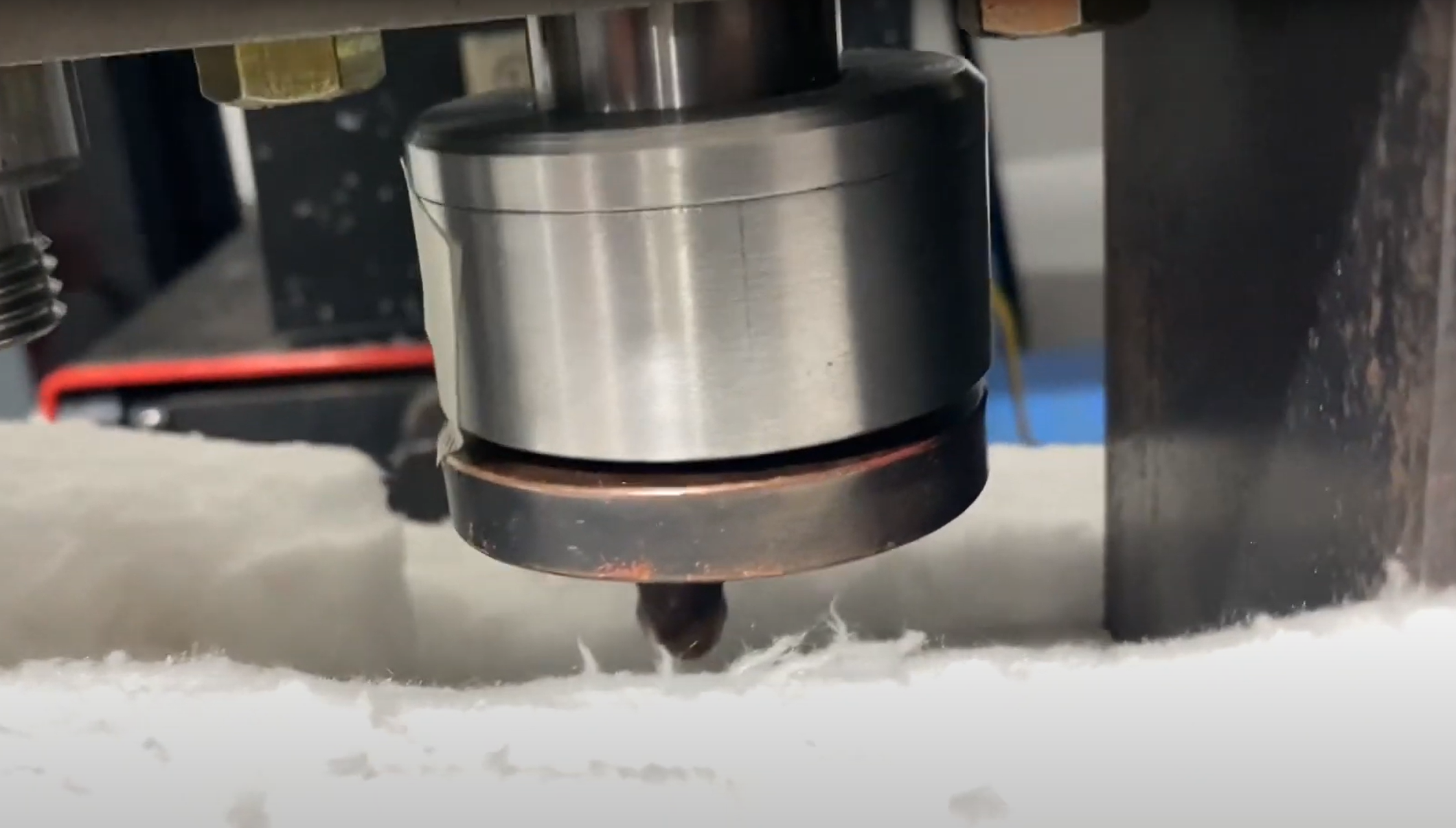
Subscribe to our YouTube Channel