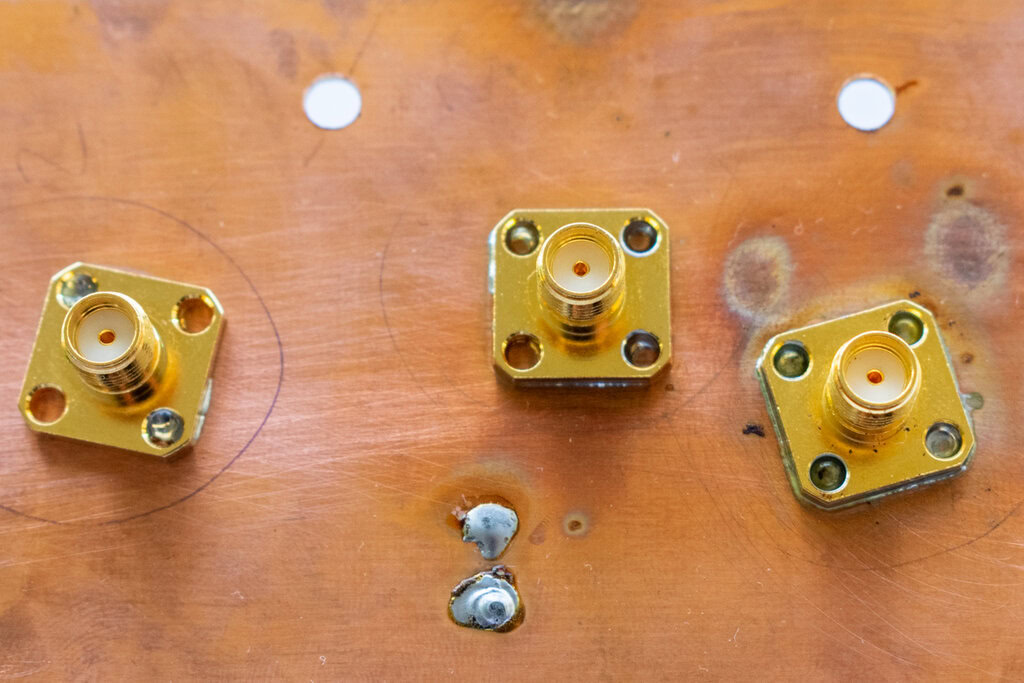
Objective: The objective of this test is to see how induction heating can improve energy.
The parts are coaxial connectors from brass that solder to 10 cm to 30 cm diameter copper discs without melting the dielectric component inside nor separating the copper plate from the substrate. The copper plate is 18 micrometers thick.
Industry: Manufacturing & Automation
Equipment: Our UltraHeat S – 2 kW Induction Heater equipment was used for the application tests.
Process: For successful soldering tests, we set induction heating equipment to 800W, and a heating cycle continued until the flow of the alloy was observed. With these settings, we achieved heating cycle times of 9-10 seconds.
When we finished the tests, all connectors were checked electrically. All samples passed the test, as the Teflon insulation wasn’t damaged during the soldering cycle.
Benefits: A custom design inductor will improve the overall process and the heating times and prevent unnecessary damage to the plate.
We recommend that a solder paste is used rather than an alloy in the form of wire. That can significantly improve the process and guarantee the distance between the details and the coil.
The process can be easily semi-automated (or entirely).
Reference Info: Application Note 3464-7399
Read more about other induction soldering applications.
To request more information about this Application note, please get in touch with us.
Subscribe to our YouTube Channel
Video