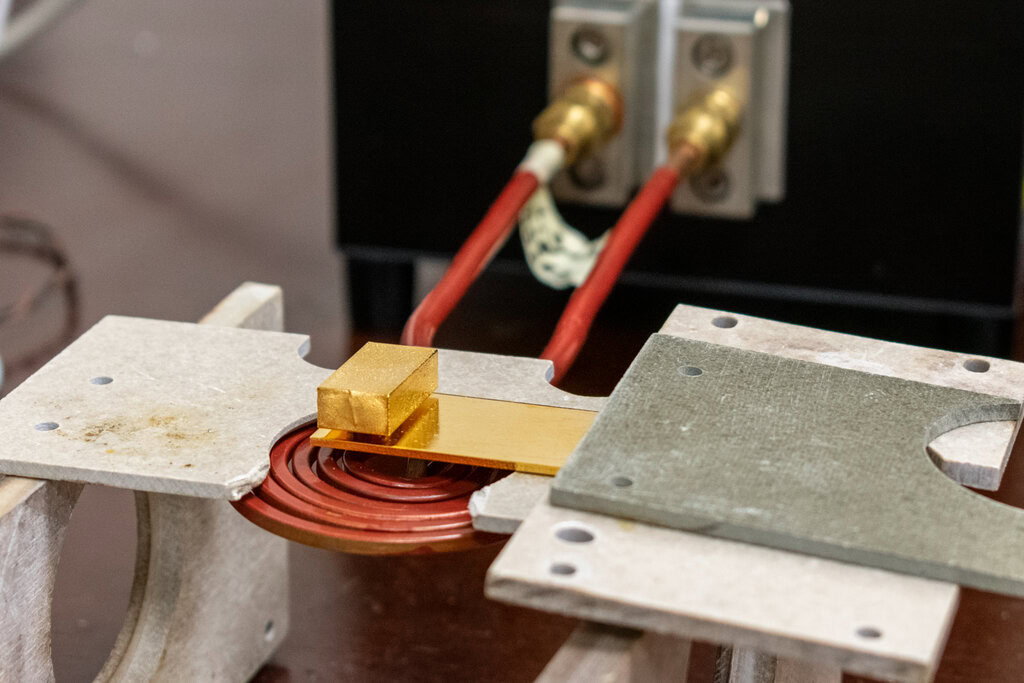
Objective: An aerospace company is evaluating the compatibility of induction soldering on their optomechanical parts. They want to implement an innovative technology process and need us to develop and demonstrate the feasibility of induction heating to solder an aluminum plate to a glass block. This application test aims to verify induction soldering of the parts with a max temperature of 300°C and achieve a heating cycle time as short as possible.
Industry: Aerospace & Defense
Equipment: To confirm all the desired objectives, we used an UltraHeat S – 2 kW Induction Heater with a water-cooled heat station and a pancake induction coil.
Process: Glass has one of the lowest thermal conductivity of a solid, mostly due to its lack of ordered crystal structure. To be able to solder glass to aluminum parts, we had to metalize them by coating them with gold, nickel, copper, and silver. This coating will be able to withstand the thermal expansions and will not be peeling off the glass surface.
Tests were made with ~501 W of power and 280°C of temperature for 15 seconds. The temperature of the soldered details was regulated via an IR pyrometer.
We recommend the use of solder alloys with lower melting temperatures and adding a flux.
Benefits: The used induction heating system can achieve an even faster heating cycle, but it is crucial to avoid overheating the parts. If a proper fixture is designed and the pyrometer guarantees the temperature, faster heating cycles will be possible.
Reference Info: Application Note 3464-7040
Read more about other induction soldering applications.
To request more information about this Application note, please contact us.
Subscribe to our YouTube Channel
Video