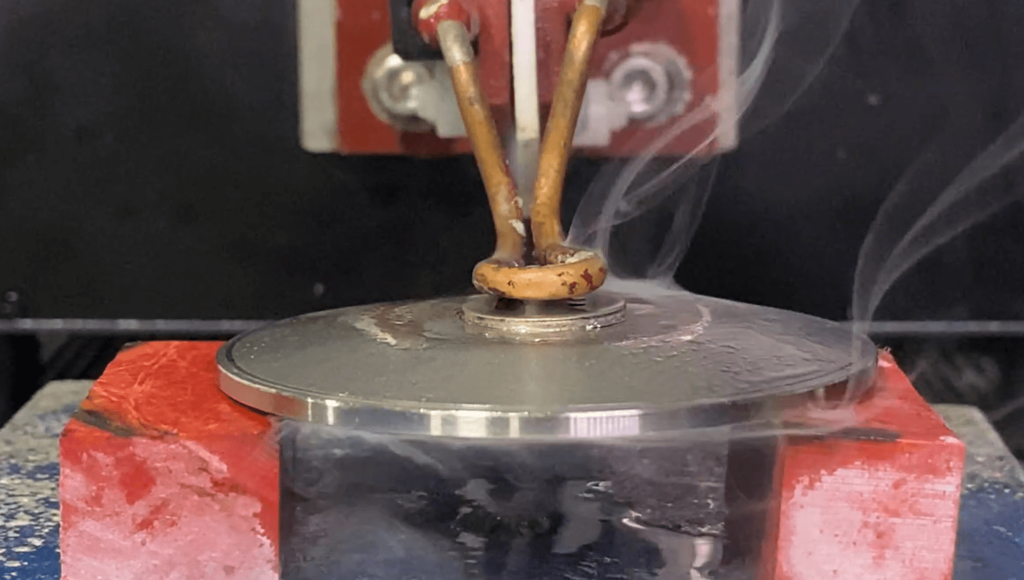
Objective:
Electronic manufacturer is looking to improve the way they solder electrode assembly by using induction heating instead of flame heating. The soldered workpiece is part of a pressure differential system that has sensors for air and non-compatible gases. Induction heating will provide focused heat and quick cycle time, thus optimizing the induction soldering process for better efficiency.
Equipment:
UltraHeat SM 5 is the recommended induction heating equipment for similar applications for its wide frequency ranges. It successfully achieves the desired productivity rate of 3 seconds per soldered part.
Industry: Electrical Components
Process:
Our goal is to solder a 0.25″ (6.35 mm) pin to a circular 2.5″(63.5 mm) stainless-steel plate which is .040″ (10.16 mm) thick. Before we begin the induction soldering process, a solder ring is placed under the joint. Then a high acid flux is applied around the solder joint location. This type of soldering flux is necessary because it will help clean the joint of any residual oxides which would prevent a good connection to be made between the parts. The heat is intentionally focused onto the head of the pin in order to transfer the heat down. This way it is concentrated only where it needs to be and heat spread to other areas of the part are limited.
Read more about other induction soldering applications.
To request more information about this particular Application test, please contact us.
Reference Info: Application Note 3463-6821
Subscribe to our YouTube Channel:
Videos