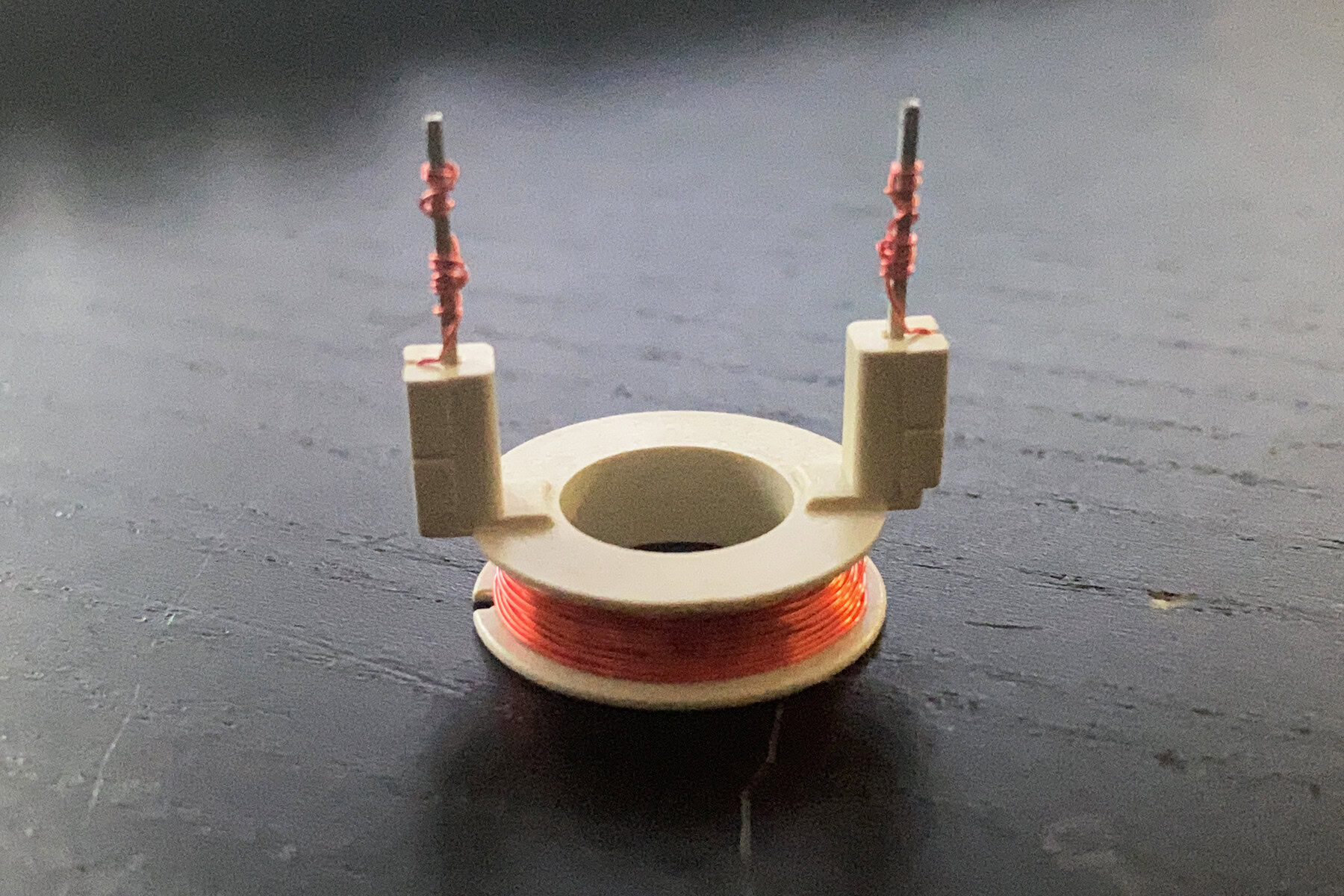
If you have ever tried soldering copper wires to steel pins, you might have found the process to be very difficult. Soldering copper wires to a steel pin is a difficult task, and the most common method used in electronics is by soldering with a soldering iron. This process is very difficult, and usually takes a lot of time, but with the induction heating method, it can be made much easier.
Objective:
A manufacturer of coils for the electromechanical, electromagnetic and electronic industries provided samples of wound coils and cables to be tested for soldering with induction. The main goal of this test is to solder both joints simultaneously within a few seconds to one part.
Industry: Electrical Components
Equipment:
UltraHeat SBT – Our high frequency system is specially designed for soldering and brazing of small components and parts such as cable end connectors.
Process:
When soldering a wire to a steel pin, the steel pin must be heated up to approximately 420C (800F). This temperature is needed to melt the solder and make it stick to the steel pin and wire. This temperature can only be reached using a soldering iron.
With induction heating, the steel pin and copper wire are placed into a coil of wire, and a high frequency voltage is applied. This causes the iron in the steel pin to heat up to 420C (800F). Once this temperature is reached, the solder can easily melt onto the steel pin, making the whole process much easier.
Benefits:
Induction heating is much faster than conventional soldering with an iron and can be used for many different types of materials. This process is very efficient and can be used by anyone.
Read more about other soldering applications.
To request more information about this Application note, please contact us.
Reference Info: Application Note 3463-6927
Pictures
Subscribe to our YouTube Channel
Video