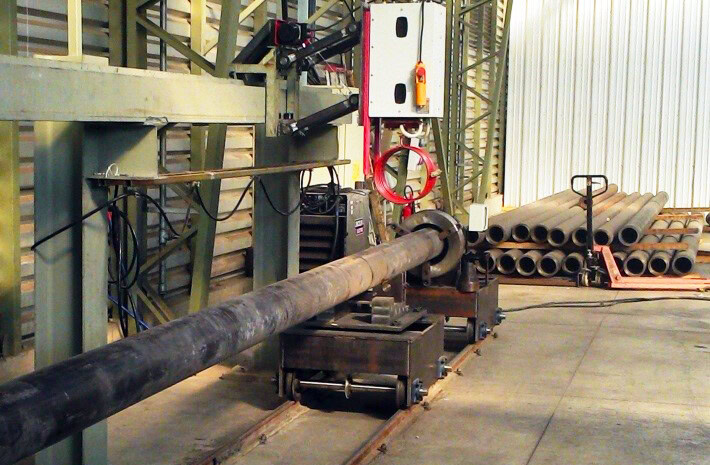
In today's mining and oil exploration, expensive stainless-steel pipes are being replaced by regular steel alloy drill-pipes. From the recently discovered sea fields to the pre-salt layer zone 7 km below sea level in Brazil, these changes are taking place. The regular steel drill-pipes are welded every 12 meters and are coated with a special epoxy.
Regular welding is not as effective for walls thicker than several centimeters. These pipes must be preheated for the welding process to be effective. The most used preheating methods are electrical resistive, gas flame, and induction heating. Oil and gas pipeline manufacturers and installers are turning to the fast, accurate, and uniform heating of induction heating systems.
For butt welding, induction heating is commonly used to preheat the joint area to 150-300°C (depending on the WT). This preheating prepares a consistent, quality weld, significantly improving fluidity and quality. After welding, the joint area can be heated to 600-650°C for thermal stress relief of the welded area.
Traditional gas flame or resistive heating systems can also be used, but are often impractical when higher temperatures are required. Not only are they too slow to meet the cycle times demanded by the industry, but also the heating can be inaccurate.
Only induction heating can guarantee uniformity around the full circumference and bandwidth of the weld joint. Among the three energy sources mentioned above, induction heating requires the least amount of time for preheating, has the highest energy efficiency, and is the safest and most cost effective. Perhaps most importantly, while the costs of induction equipment are higher at the beginning, the efficiencies offered will offset the added cost. The better and safer environment for workers will help optimize both productivity and quality.
Other benefits of induction heating include:
- Variable control over temperature/time parameters. Minimal damage of factory coating and no deleterious surface residues.
- No open flames or exposed heating elements.
- Reduces energy costs and eliminates the needs for large gas storage area.
Pictures:
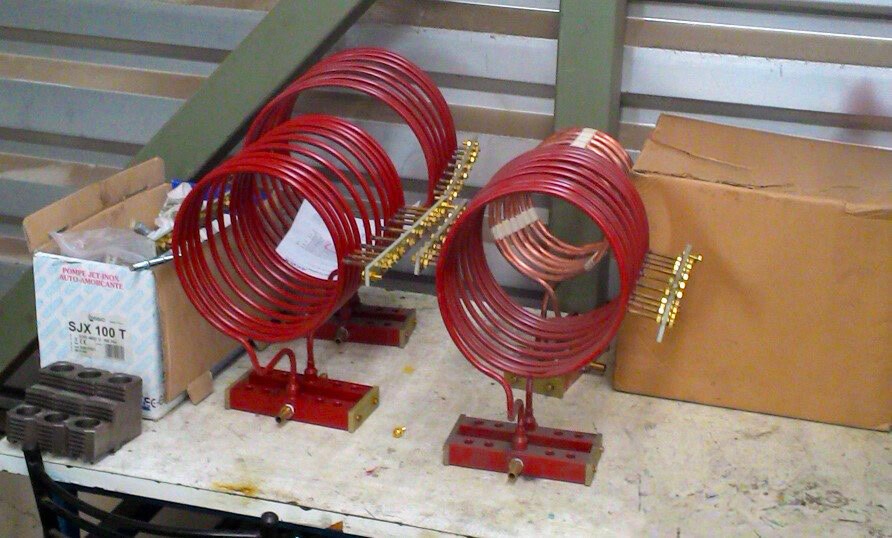
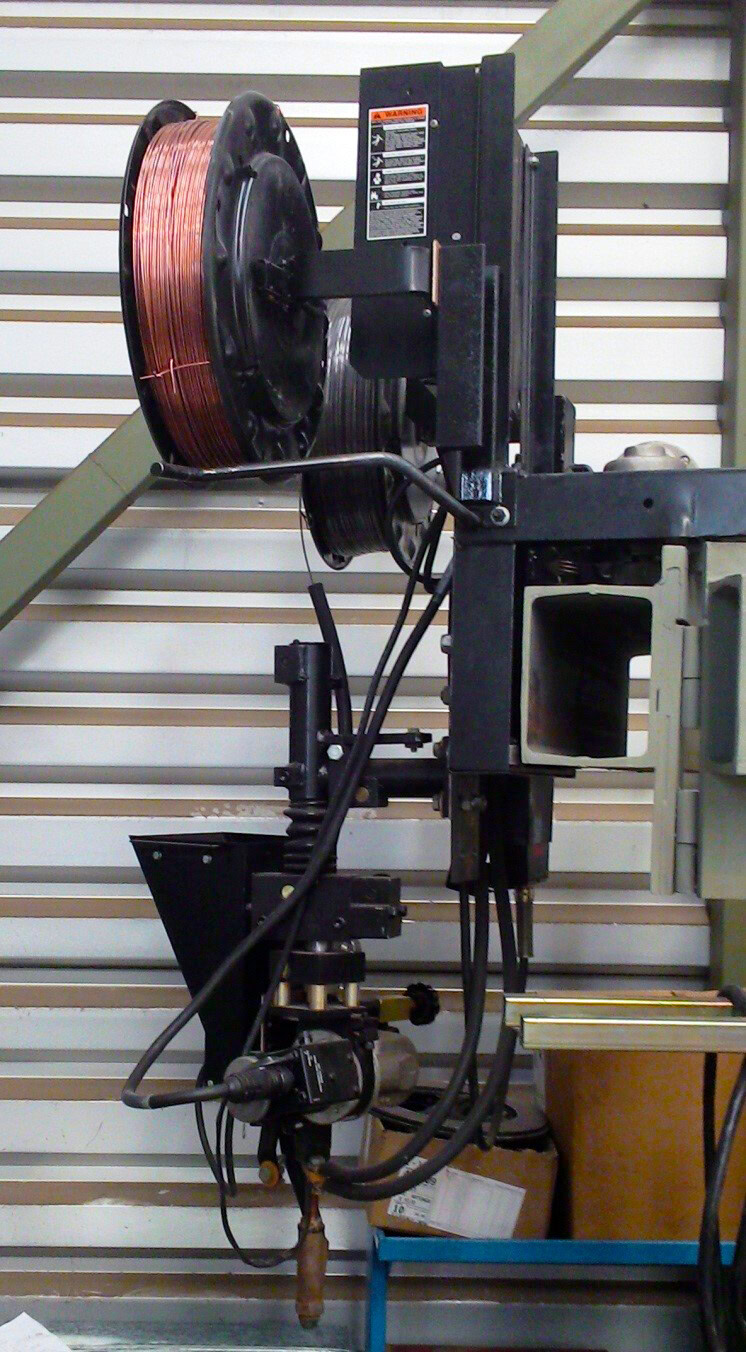
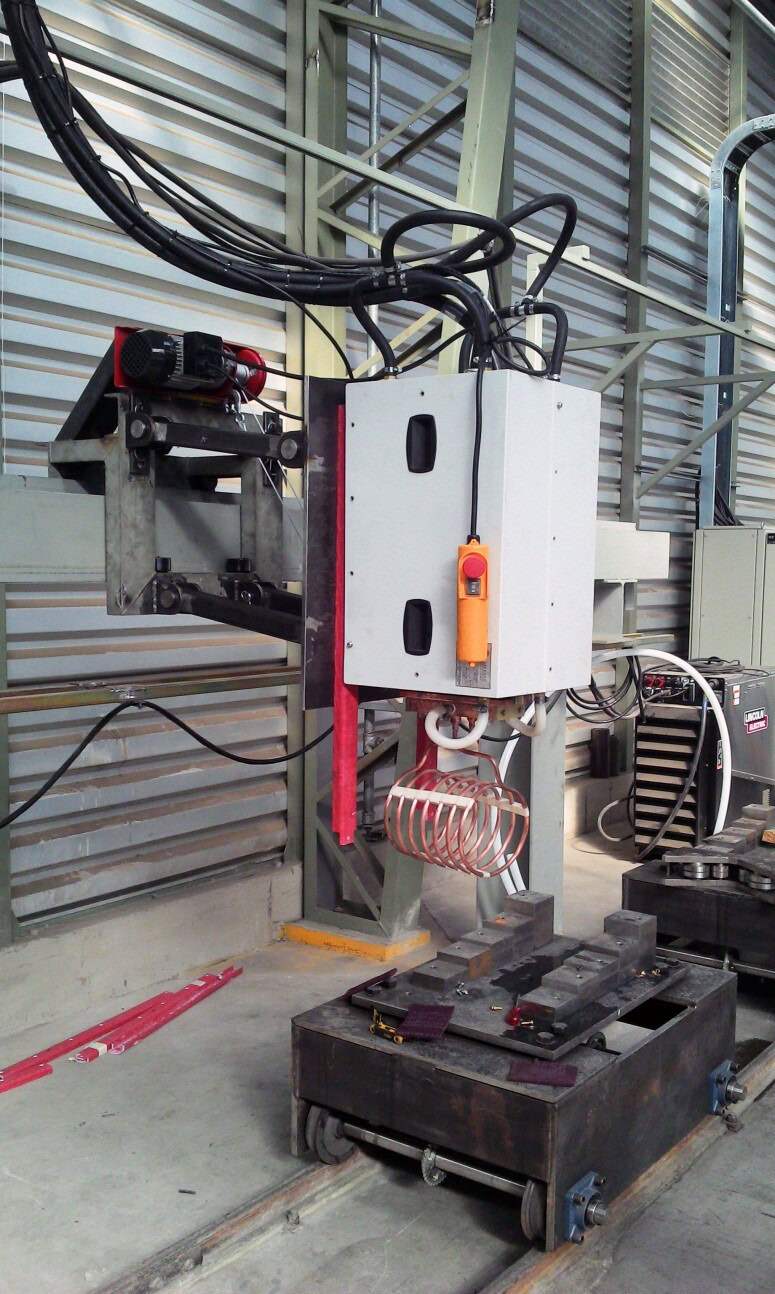