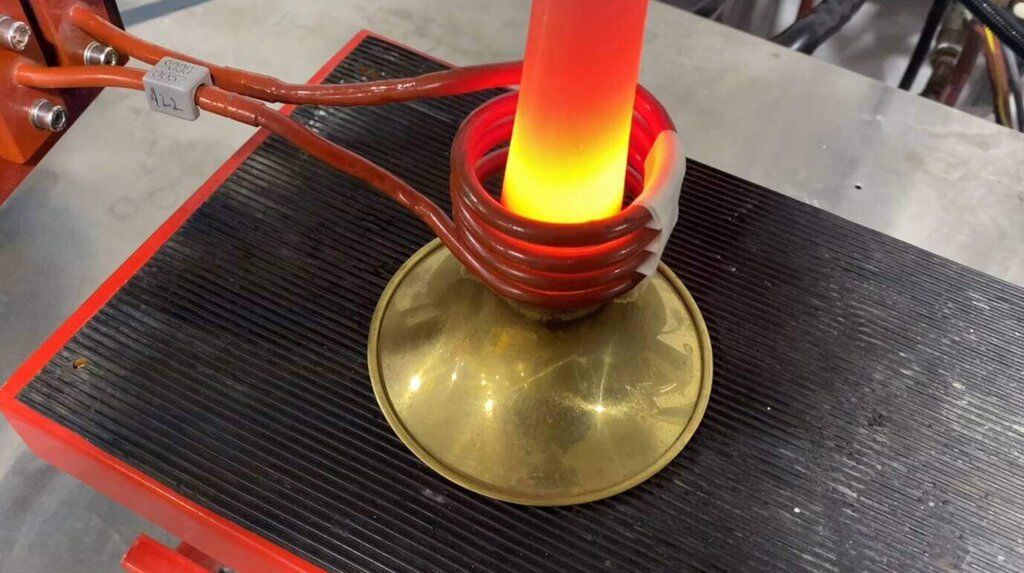
Application: Annealing
Industry: Manufacturing & Automation
Application Objectives: A musical instrument manufacturer is looking to replace their torch annealing with induction equipment. The low-cost induction unit they purchased before does not allow for automation, so they turned to UltraFlex for a more advanced solution for their annealing process. The main objectives are to ensure better quality and consistency of the results, determine how fast each part can be annealed, assess the ease of swapping out coils for various parts, understand the reaction to brass versus nickel silver, and evaluate how the annealing process affects the large flare end of the French horn part. Reducing timing and increasing productivity are essential goals
Equipment: Solo 12, HS24, multiturn coil
Materials: Wind instrument made of brass and nickel silver
Process: There were two tests. Both tests had the same power set point of 60% of the power output, but different frequency. For Test 1 an UltraFlex multiturn lab coil was used and the temperature was set to +1000°C. The heat cycle time was relatively short, lasting 1 minute and 38 seconds. For Test 2 the temperature was slightly lower at +800°C, but the frequency was higher. In this case the heat cycle time was a bit shorter, lasting 1 minute and 30 seconds but temperature limitations were kept.
Results and Conclusions:
The Solo 12 system is well-suited for this application, as demonstrated in the video. We employed a cobot arm during the tests to highlight the automation capabilities of UltraFlex equipment and to facilitate future flexibility in switching to the brazing process, thereby optimizing the entire production line. This allowed us to address the customer’s primary concern: the system provides variable power outputs that can be adjusted throughout each cycle, accommodating differences in part thickness.
Reference Info: AR 3463-7707
Pictures
Subscribe to our YouTube Channel
Video