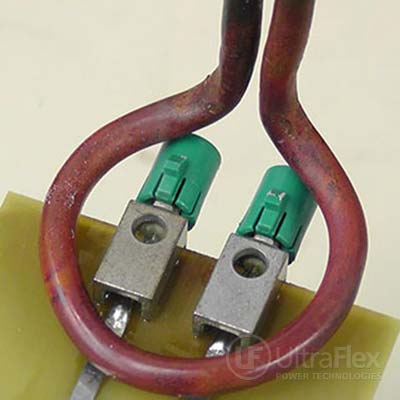
soldering end connectors
Objective
Use induction to simultaneously solder end connectors to a printed circuit board within 120 seconds. The process must ensure a good solder joint for the component feet and the center pin conductor, which is shielded by the conductor body. The customer requirements allow for the soldering of the feet and the center pin in two separate steps; however, only a single coil can be used. The current process using a traditional soldering iron currently takes the customer 25-30 minutes.
Equipment
UltraHeat SM2/200 and HS-4WHS-4 Heat Station
Materials
• Single turn induction coil, with approximate 1.2″ (30.48mm) diameter, made from 3/16” (4.7625mm) diameter tubing connected to 3/16” (4.7625mm) flare fittings.
• Solder alloy Sn 96.3/Ag3.7
Key Parameters
Temperature: just above 450°F (232°C)
Process:
- Solder paste is applied over the mounting holes on the top side of the PCB and brushed into the holes so that the part feet carry the alloy down the plated hole when assembled.
- Following this, a line of alloy is placed on the single line trace on top so that the inside connector is pushed into the solder paste.
- The assembly is placed in the coil, positioning the coil above the components. The UPT-S2 Power Supply is turned on. After several tests, it was determined that 33 seconds is the ideal time to produce a good solder joint, while not overheating the components.
- The component body acts as a heat-carrying susceptor, causing the solder to flow and the solder joint to be created. NOTE: It is important for applications considering this type of soldering solution to ensure that the component is rated for the temperature that is reached during the soldering process.
Results/Benefits:
- Power on demand – rapid heat cycles
- provide for uniform heat distribution on the mating components at the solder joint eliminating “cold” joints and incomplete solder alloy flow
- Repeatable process, not operator dependent when parts are set in a nest or fixture
- Allows for the use of pre-measured alloy rings or paste, which reduces costs associated with wasted material.
Pictures
Video
Request information or contact us about this application.