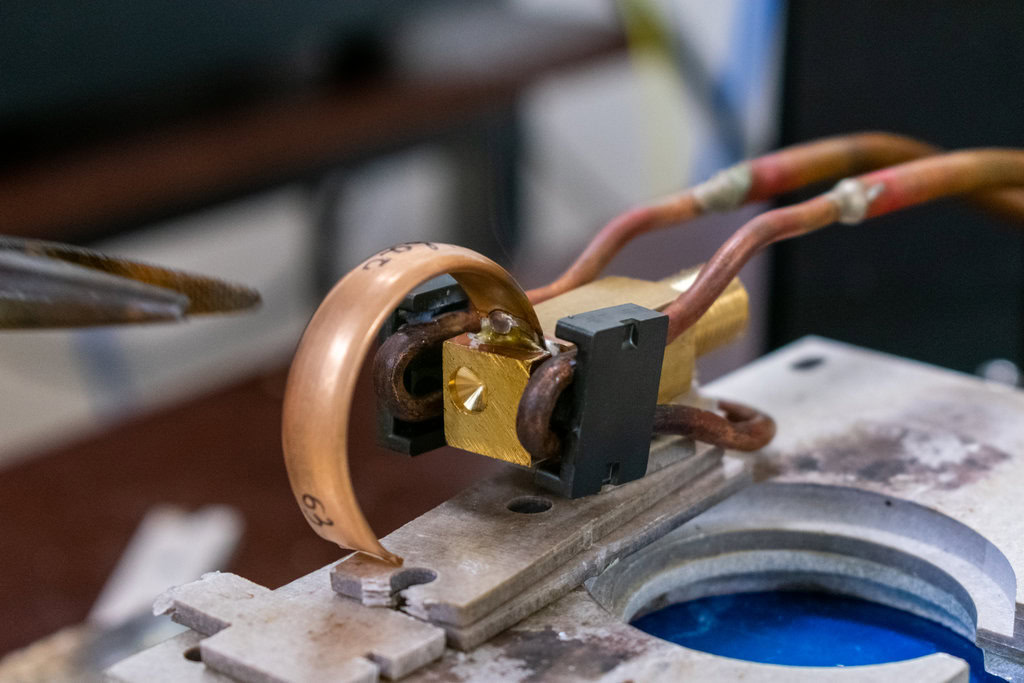
Application: Induction Soldering of Bourdon Pipe to Brass Body and Cap for Manometers Production
Objective: We were tasked by a manufacturer of manometers to test the induction soldering of a bourdon pipe to a brass body and a cap using an efficient and reliable process. The client’s key requirement was to achieve a maximum heating cycle of 6-8 seconds per joint while ensuring a good and reliable solder flow without overheating the bourdon pipe.
Industry: Manufacturing and Automation
Equipment: We utilized a SOLO Induction Heating System.
Process: Our application engineers conducted multiple tests with different settings on a SOLO 12-kW system, resulting in heat cycle times of 4, 7, and 8 seconds for different-sized parts.
Fixtures are strongly recommended for production to ensure the pipe’s proper positioning inside the coil, preventing displacement during the soldering process and achieving repeatable results. For successful tests, we used a C-shape Coil.
Benefits: Our induction soldering process demonstrated to the customer the advantages of using induction heating equipment for their manometer production. By investing in this technology, the client will enjoy greater process control, increased repeatability, improved productivity, and enhanced energy efficiency.
Overall, our induction soldering process for manometer parts is a reliable and efficient solution that can benefit manufacturers in various industries.
Reference Info: Application Note 3464-7776
Read more about other induction soldering applications.
To request more information about this Application note, please get in touch with us.
Subscribe to our YouTube Channel
Video