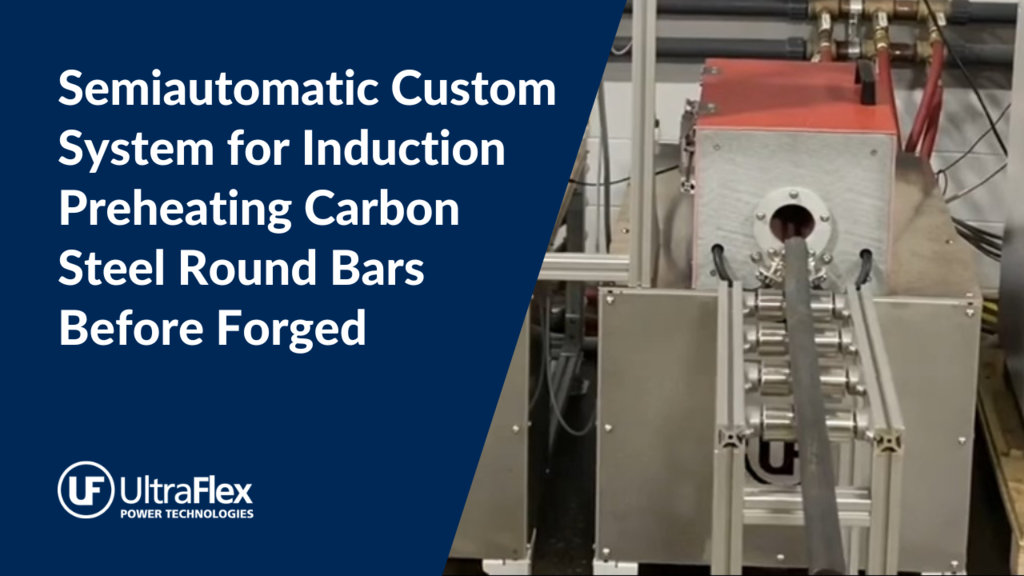
Review the latest development at UltraFlex Power Technologies.
You can see our semiautomatic custom system built to preheat carbon round steel bars before forging. The system is designed to allow quick coil changes to work with various length diameter bars. The PLC allows minimal input by the operator to streamline the process and speed up production.
The purpose behind the two heating stations is to eliminate downtime during bar changes. The second bar is heated immediately after the first one is done, given it is in position beforehand.
The principal operation is the following: the system can be controlled in two modes – manual and automatic. The manual mode does not require operator input between each stage of the process and will only be used for maintenance procedures. The automatic mode, used in production requires the bars to be inserted into position on time.
The operator panel has an emergency stop button, on-off switch, temperature display, and light towers for each heat station. A solid green light indicates that the system is ready to heat, solid red light indicates that the heat function is disabled. A solid amber light indicates that the heat is on. Blinking amber light indicates that the soak cycle is finished, and the part can be removed. A blinking red light indicates that there is a system fault.
Before the demonstration in this setup, we predetermine the target temperature and the soak time. Once these two parameters are predetermined, we select main which will return to the primary operations.
We run the system to demonstrate operation. As you can see, before we ran it, both rods are pulled outside the furnaces. Press the on-off switch and enable heating operation. As soon as the rod is inserted, the proximity sensor will recognize, and the power supply will start the heating cycle. We are also pre-inserting the second rod, which will be heated once the heating of the first one is finished. You can see the power output and the amount of power delivered to the rod.
The pyrometer is registering temperature. The lowest it will measure is approximately 700°C degrees. Our set point is 1200°C degrees. Once that temperature is registered, the PID controller will kick in and reduce the power output until the power reaches 1200°C degrees.
There you can see the timer of five seconds. Our soak time is only set to five. Once the soak time is over, the amber light blinks, indicating that the part is ready to be pulled out. Once the part is pulled out, the second one is heated and started to be heated immediately. In the production setting, the operator would have already inserted the second part into the first heat station. Once this one is finished, the changeover switch will switch to power from this power supply to the second, and the cycle will continue.
Subscribe to our YouTube Channel
Video