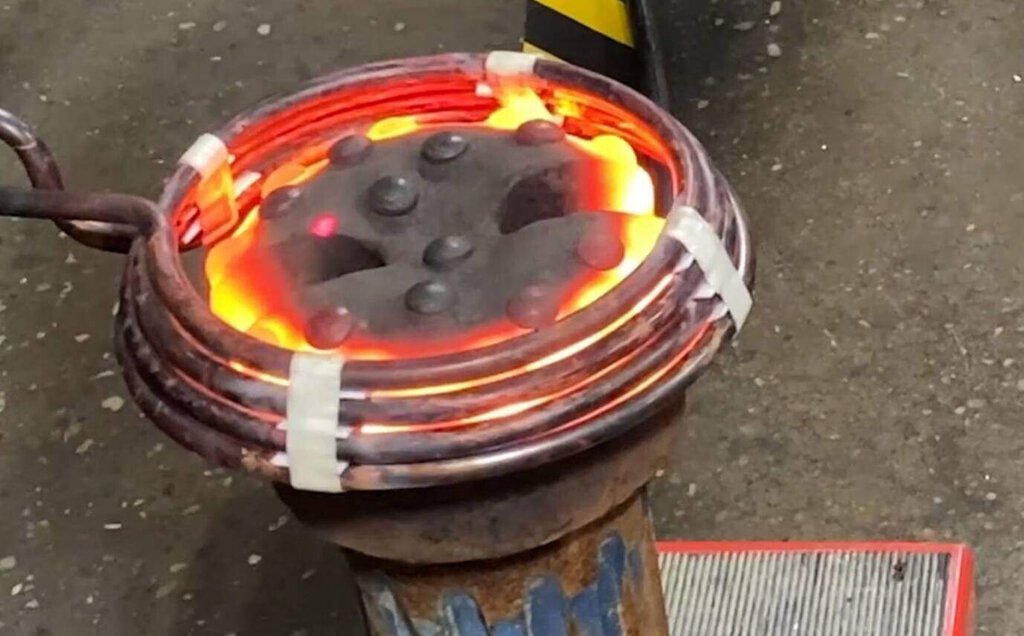
Application: Preheat & Post heat
Industry: Hand Tools & Mining Industries
Application Objectives: A customer involved in recycling carbide drill bits from old tool steel billets is seeking to replace their current coal-driven furnace with a more energy-efficient, time-efficient, and environmentally friendly method.
They shared: "The current process is messy and requires storing and purchasing coal, which we want to move away from."
To develop entirely new process and technology UltraFlex had several challenges ahead:
- Determine the power required to heat the bits in under 300 seconds (about 5 minutes).
- Determine heating profile needed to heat the bit and remove the tips.
- Increasing productivity rate.
- Improve safety or energy efficiency.
- Design custom helical coil
Equipment: Smart Power™ 50 kW, 10-60 kHz with HSP-100M heat station, helical coil
Materials: Steel Drill heads, larger sizes, 3-7.5" OD, failed drill heads for carbide recovery, head of the tool.
Key Parameters:
- Max Temperature: 1500°C
- Heating cycle – 60-300 seconds (about 5 minutes)
Process:
Button carbides are pressed fit and brazed in position but require similar temperature to remove. As the part is big, the temperature reached would be different in the different zones of the steel head, so we would need several heating cycles for the different zones. We conducted 3 tests.
- Test 1 – 8.5" Diameter bit – 100 % set point
- Test 2 – 6" diameter bit – 80% set point, 880o C
- Test 3 – 6" diameter bit – 70% set point 900o C
The first test used an 8.5" diameter bit at 100% power, with small adjustments made. The second test used a 6" diameter bit at 80% power, reaching 880°C, and most buttons were removed in the first heat cycle. In the final test, despite a lower power setting, the temperature reached 900°C, and almost all buttons were removed in the first heat cycle.
Results and Conclusions: The 50-kW low frequency Smart Power system was used for testing these parts. Overall, the parts heated easily, and we were able to recover most of the carbide tips during the 1-st or 2-nd cycle. The current process requires proximity to open flame and 20-minute heat cycles where we were able to perform the cycles in 1:30 min on the smallest bit. Another benefit of this equipment, it allows for multiple heating cycles if all the bits are not recovered on the first attempt. A profiled coil to allow for more heating of the center of the bit and adding pulsing of the power will help to get better results. The 50-kW low frequency smart power is a good system for this application.
Reference Info: AR 3463-8880
Pictures:
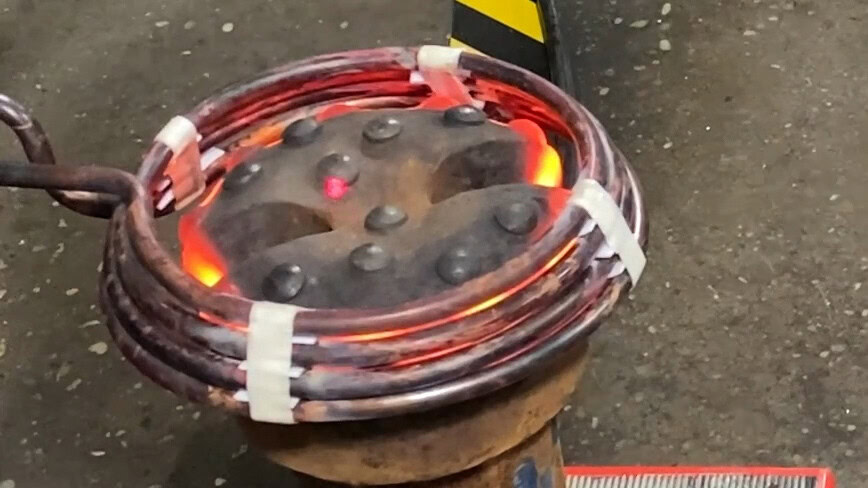
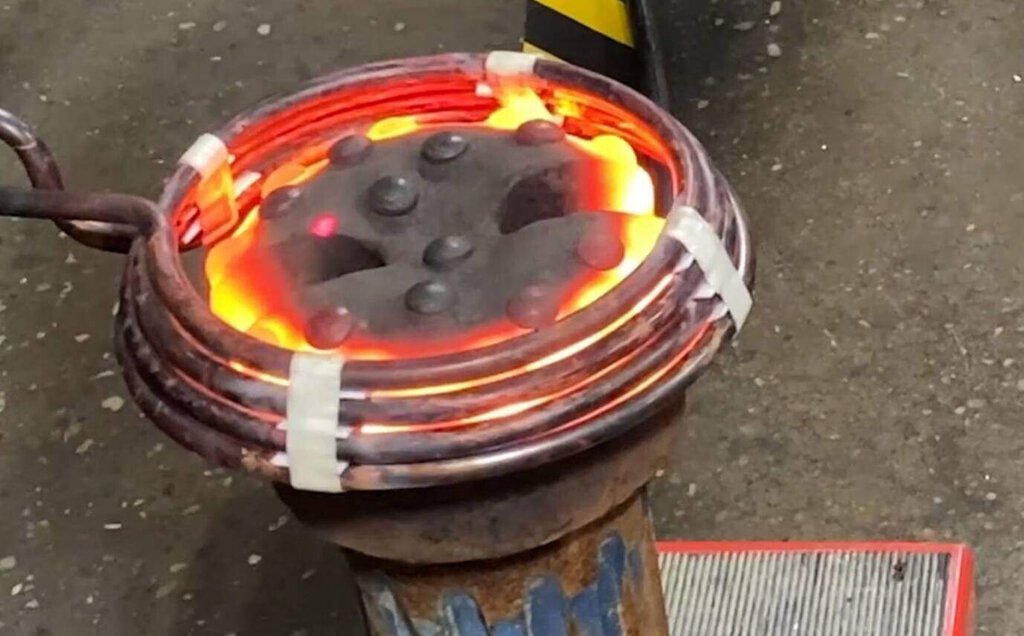
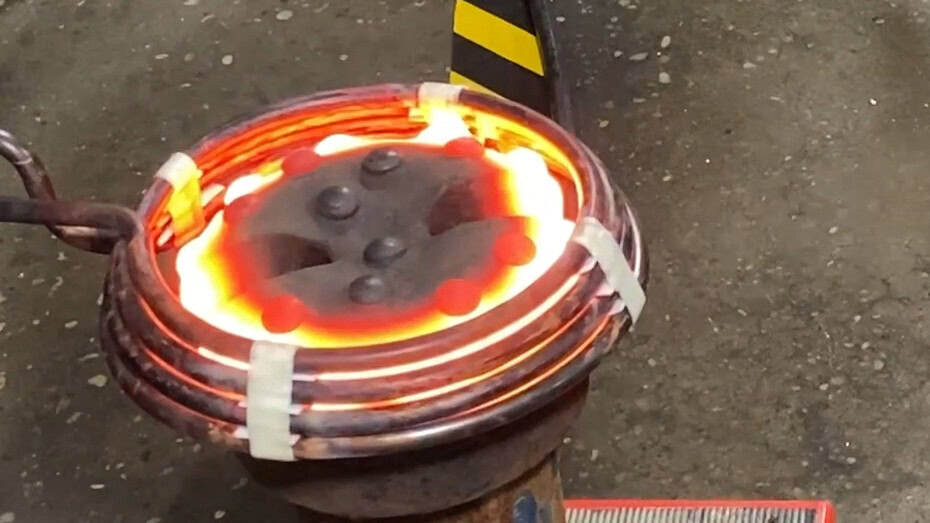
Subscribe to our YouTube Channel
Video