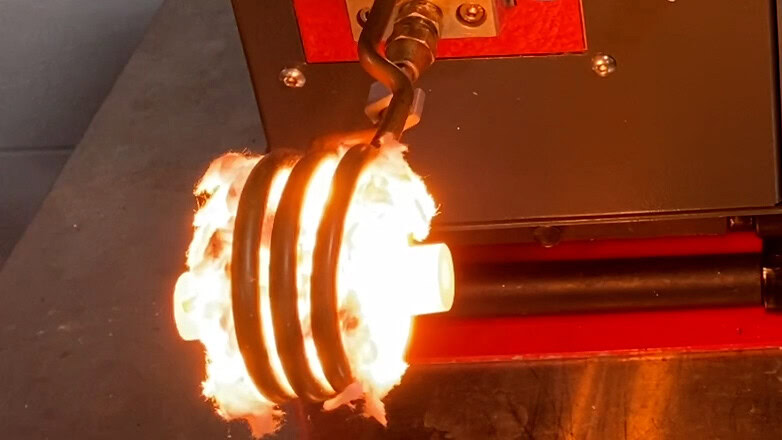
Application: Materials Research & Testing
Industry: Academic & Research
Application Objectives:
A university is researching to develop a new process of producing monolithic silicon carbide joints using silicon and carbon precursors. The precursors are modified and optimized for silicon carbide formation with the application of heat. UltraFlex was challenged to prove the feasibility of the process and to validate the material research concept. An application test in our labs should demonstrate the use of graphite susceptor for the Si-C powder and tube binding application. The aim is to join silicon carbide tubes together by applying heat to graphite susceptor and to transfer heat to the joint zone. For that we need to heat the susceptor to no more than 1500°C as fast as possible and hold the susceptor at this temperature for 5 minutes.
Equipment: Solo 10 + HS-24 + lab coil
Materials: Graphite and Sic tubes, silicon and carbon precursor, and graphite susceptor ring.
Tube/Rod dimensions:
- TC Tube – OD 16mm, ID 6 mm, thickness 5 mm
- Tube – OD 10 mm, ID 4.5 mm, thickness 2.5 mm
- Rod – OD 9.525 mm
Key Parameters:
- Max Temperature: 1500°C
- Temperature tolerance: 50°C
- Heated length or zone: 1-3/16"
- Heat Cycle: 100% duty cycle, as fast as possible to temperature
- Other requirements: 5-minute hold at temperature to cure the parts
Process:
During the first round of testing the tubes were heated inside a graphite ring and bonded in a butt joint configuration. Instead of bonding 2 separate tubes together, for our testing the customer has made a tube with slit in it that will be filled with the precursor powder and heated to close the slit.
In this new process two kinds of silicon tubes were used – 10 mm and 16 mm diameter. The power supply model was Solo-10, and the heat station model was HS-24 with a UltraFlex lab test coil. The temperature reached was around 1492°C, with the heating process taking between 24 to 40 seconds. Once the target temperature was reached, it was maintained for 5 minutes to ensure proper bonding. During heating, the power required was between 6.7 kW to 8 kW, and during the holding phase, it ranged from 800 W to 3 kW.
Results and Conclusions:
We used our SOLO power supply to test the application. The results were promising and seemed to fill the whole slit with strong adhesion to the tube. This application is feasible and will be able to work with the power supply selected.
Reference Info: AR 3463-8065
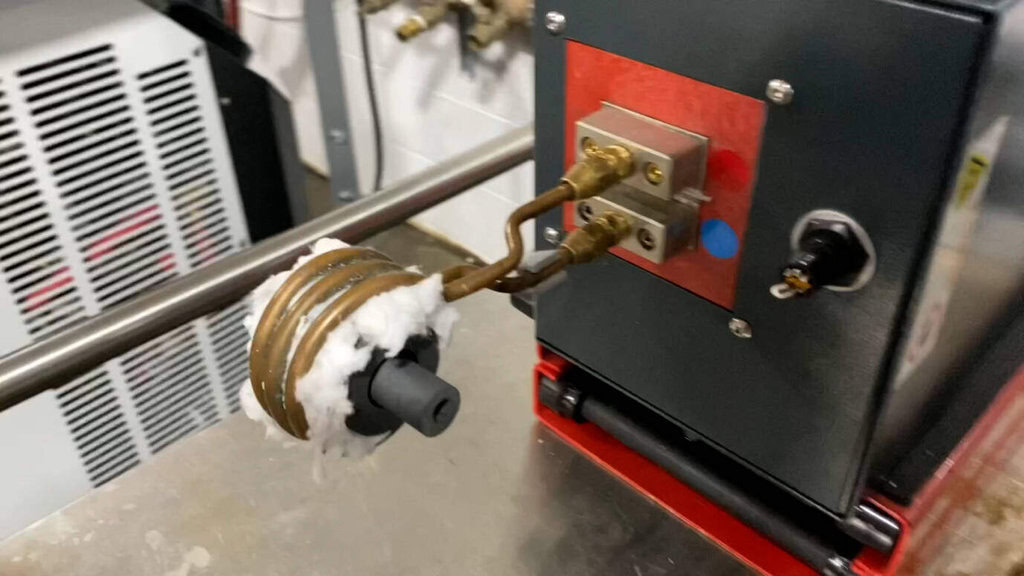


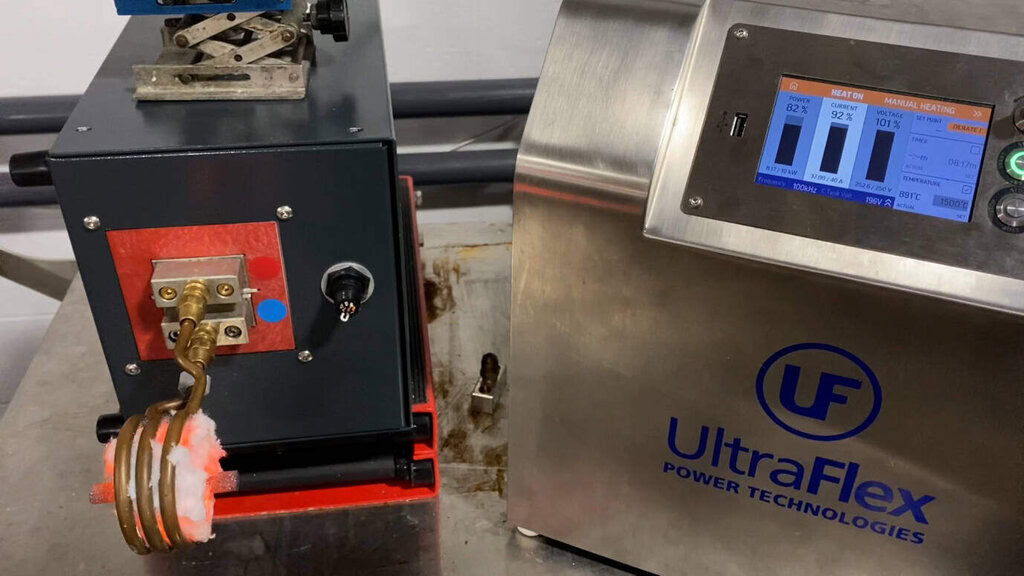
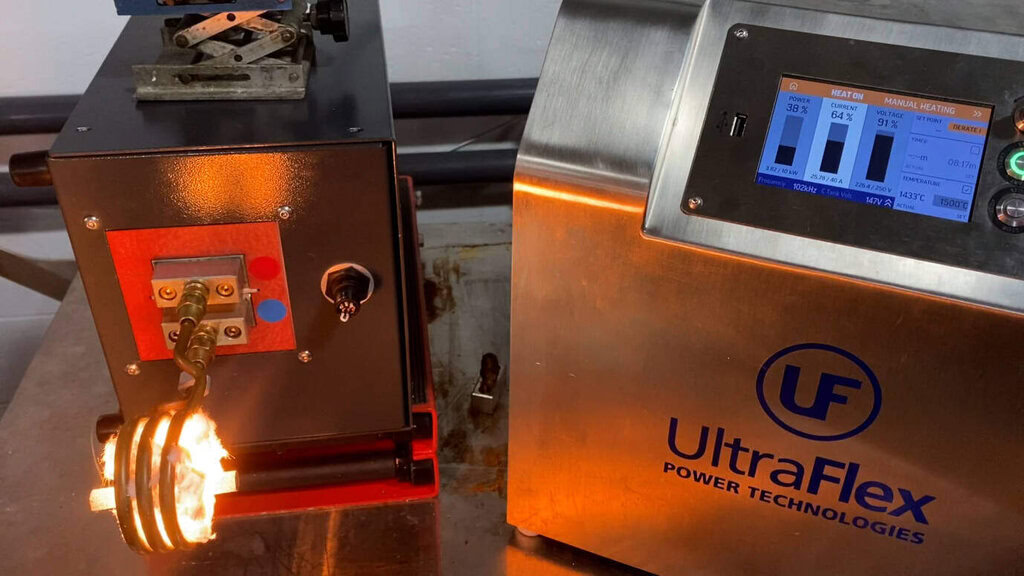




Subscribe to our YouTube Channel