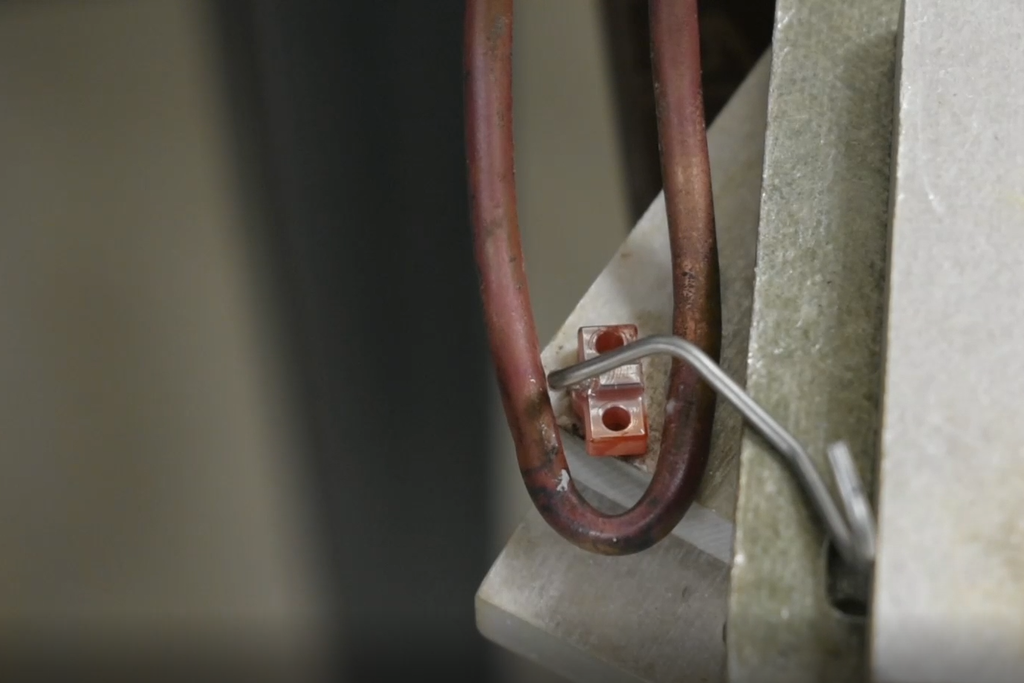
Objective: A company specializing in miniature cryogenic cooling solutions wants to replace its current technology with induction heating equipment to improve quality and reliability in the process.
The main application test objectives are to achieve excellent brazing results. The joints must be visually filled with a brazing alloy, and a max heating temperature must be about 700°C.
Industry: Appliances & HVAC
Equipment: We used an UltraHeat SBT 3kW – High-Frequency Series for this application.
Process: The heated parts are small stainless-steel fittings and tubes. One detail consists of two different fittings and one tube that must be brazed with induction.
We chose a proper insulation material to serve as a fixture and placed one of the fittings inside the coil. After the first test, we decided to use 2 or 3 brazing rings for one joint (it depends on the fitting). Enough flux was applied to the detail to ensure good protection during the brazing process.
Overall, the induction soldering application was successful in achieving the objective of improving energy efficiency in the production process. The joint was first tested using compressed air to check for leaks or if the tube had been sealed from the alloy. The assembly is brought under a microscope if the first test is passed. Under the microscope, we observe good uniformity around the joint. No cracks or shallow spots were visible.
Benefits: For this application, a custom coil will be designed along with a proper fixture for the assemblies.
The main advantages of integrating induction heating equipment in the production process are improved energy efficiency, a higher degree of controllability, increased repeatability, process control, and productivity.
Reference Info: Application Note 3464-7621
Read more about other induction brazing applications.
To request more information about this Application note, don’t hesitate to contact us.
Subscribe to our YouTube Channel
Video