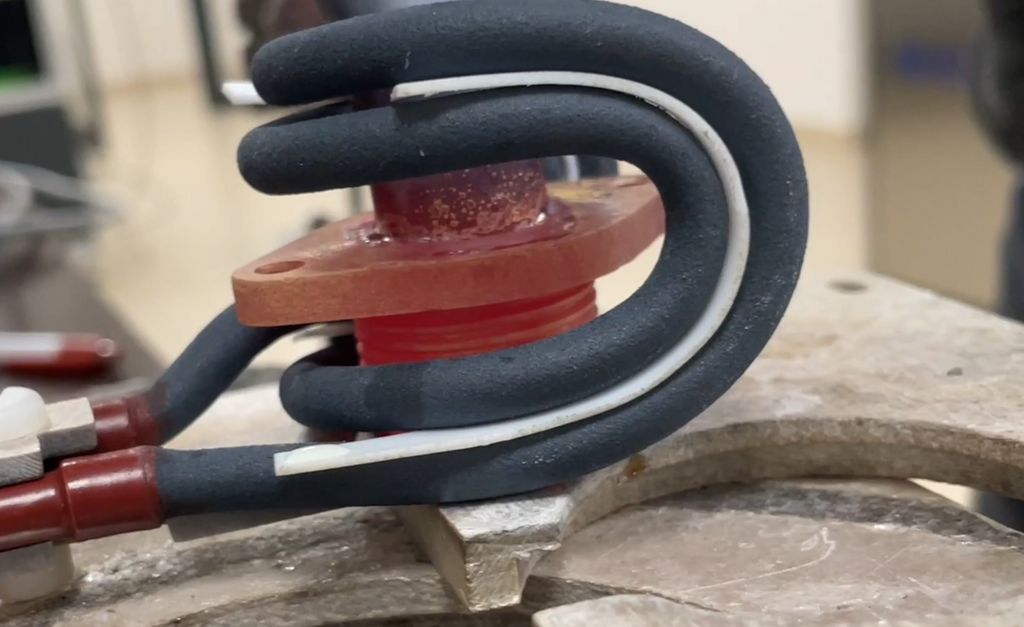
Application: Brazing
Industry: HVAC manufacturing
Application Objectives: A customer from HVAC manufacturing industry is looking to braze copper to brass with induction for 3 different assemblies. The whole brass piece is heated and one of the assemblies has a silicone part roughly 50 mm away from the joint. The brass pieces are odd shaped, and the copper pipes vary from 13-16 mm. The time requirement is to braze each assembly in less than 20 seconds.
UltraFlex team estimated that a 16kW SOLO system, paired with at least two coils, would be up to the task. The assembly with the silicone part required special attention, as it needed to be protected from the heat. This meant that fast cooling might be necessary to ensure the silicone remained intact.
With these challenges in mind, the UltraFlex team set out to fine-tune their approach, aiming to meet the customer’s needs with precision and efficiency.
Equipment: Solo 24 + HS-24W + UltraFlex Lab Coil
Materials: Copper to copper and brass to copper distributer assemblies.
Key Parameters: Max. heat cycle is <20 seconds
Process:
The testing process began with heating a small copper-to-brass assembly. Using the Solo 24 power supply, the HS-24W heat station and a Lab Coil were employed. The temperature was set to 760°C, and the heat cycle time was 12 seconds.
In the second test, another small copper-to-brass assembly was heated using the same power supply and heat station, but with a different Lab Coil. The heat cycle time increased to 17 seconds due to the lower power used.
The third test involved a small copper-to-brass assembly with a silicone part. Returning to the first levels of power and keeping the max. temperature at 760°C, the heat cycle time was reduced to 10 seconds.
Finally, the fourth test focused on a larger copper-to-brass assembly. The heat cycle time extended to 26 seconds.
Results and Conclusions:
The brazing tests were successful and good joints were achieved.
The largest assembly has a slightly slower heating cycle. As can be seen from the video, roughly 7-8 seconds from the heat cycle are from the hold stage until the alloy fully melts. Optimization of the coil is required so that the alloy melts uniformly.
The temperature regulation can be optimized to achieve faster heating cycles.
A proper fixture is required to optimize the heating cycles as well as the quality of the joint. During our tests, the assembly was held manually. This can compromise the contact between the ring and the assembly, essentially leading to prolonged heating times.
From the tests, we conclude that the appropriate power of the system is 12kW. Our 12kW SOLO will be able to fulfill the requirements for all joints.
One of the samples was cut through the joint. Good flow of the alloy was observed, and full coverage of the joint is apparent.
Reference Info: AR 3464-8272
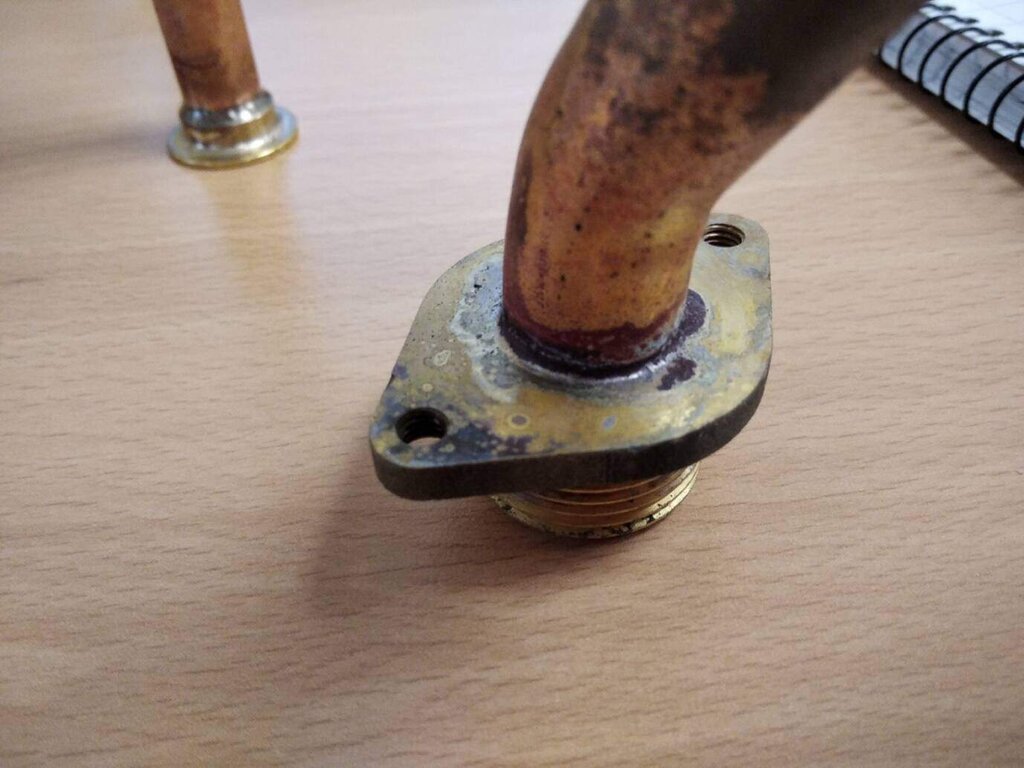
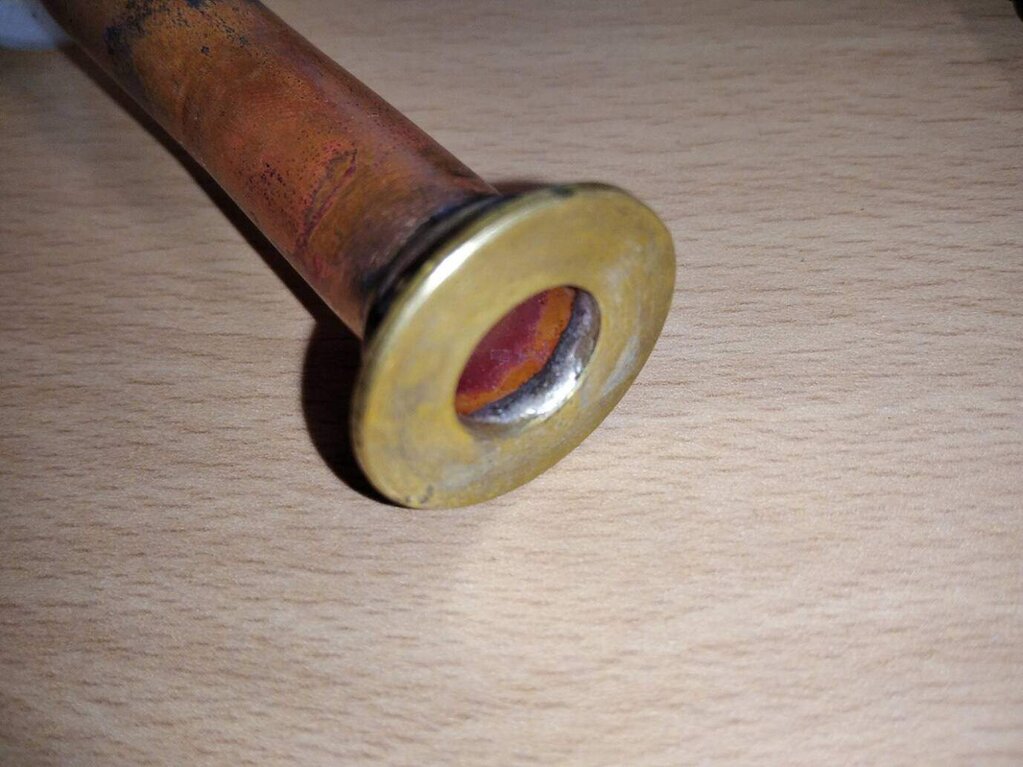
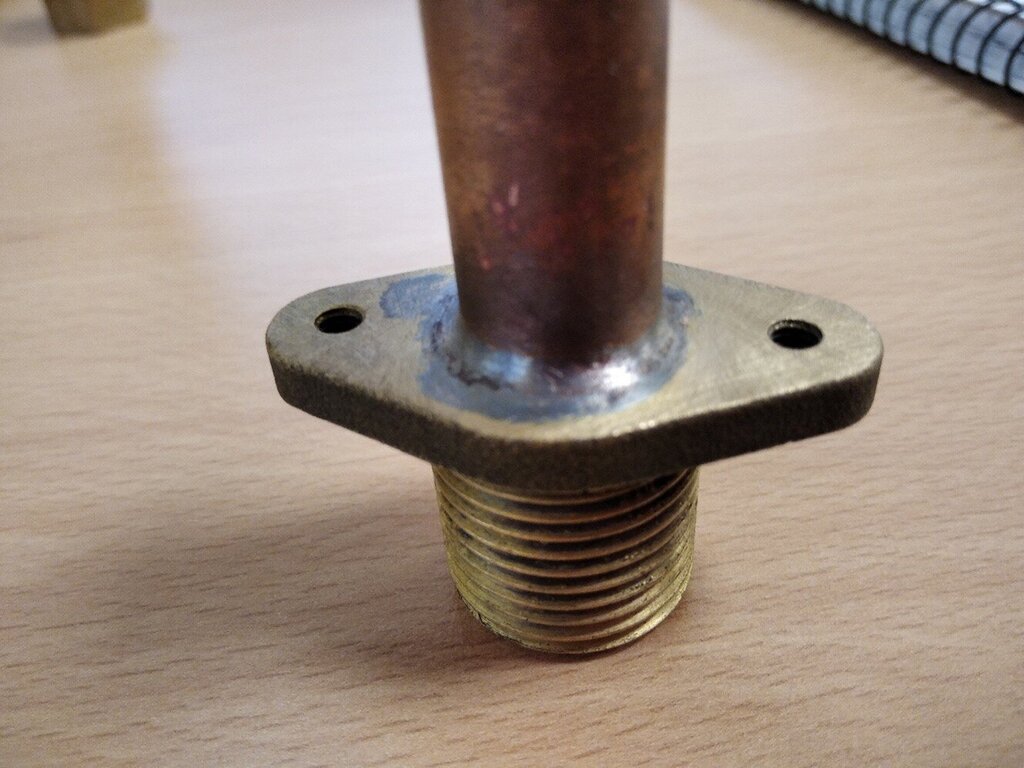
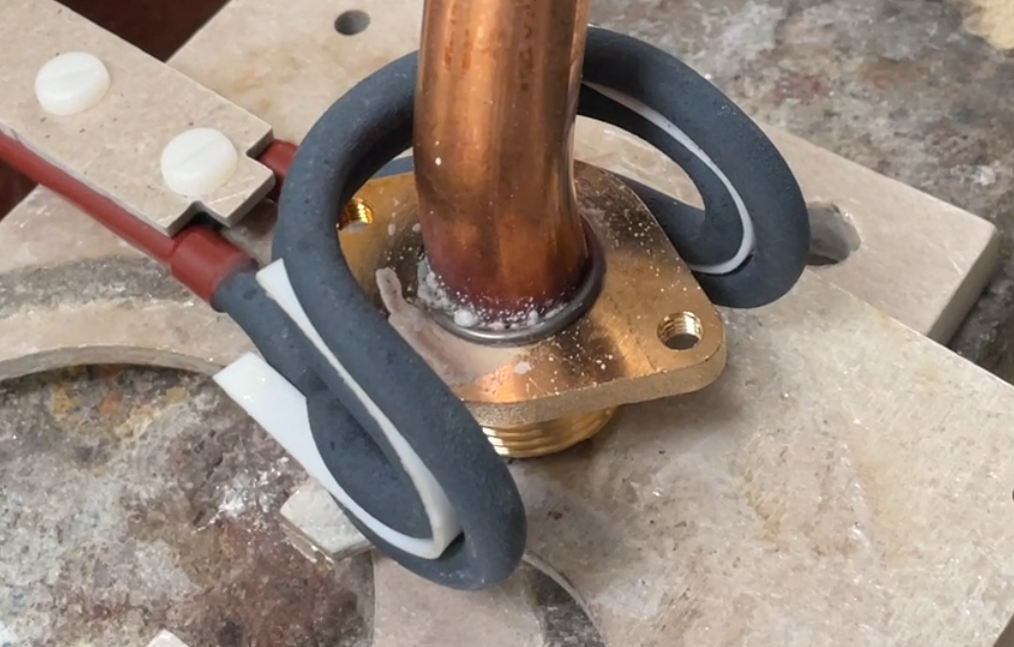
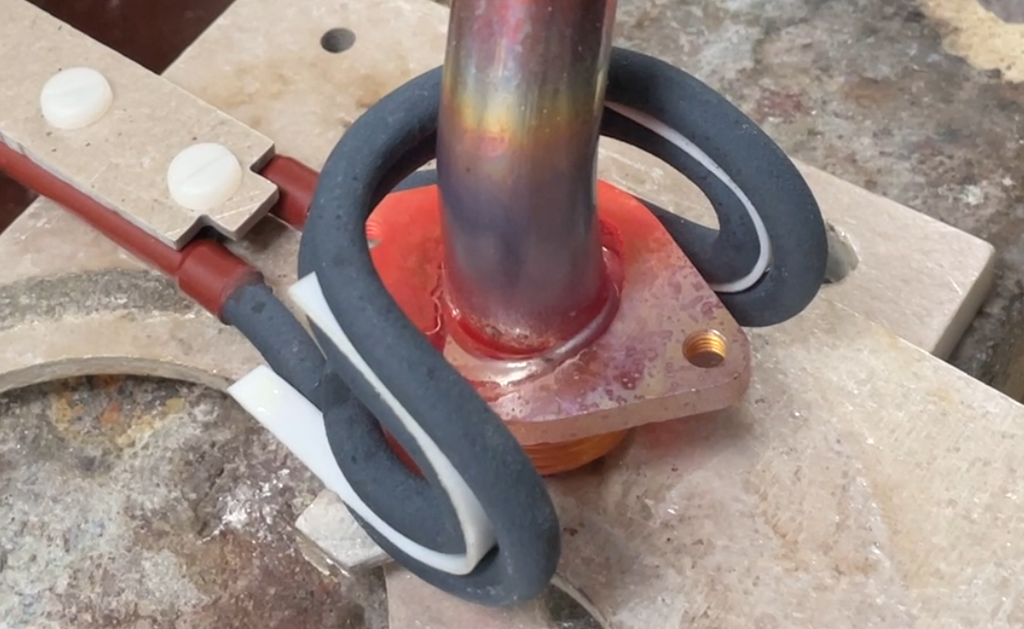
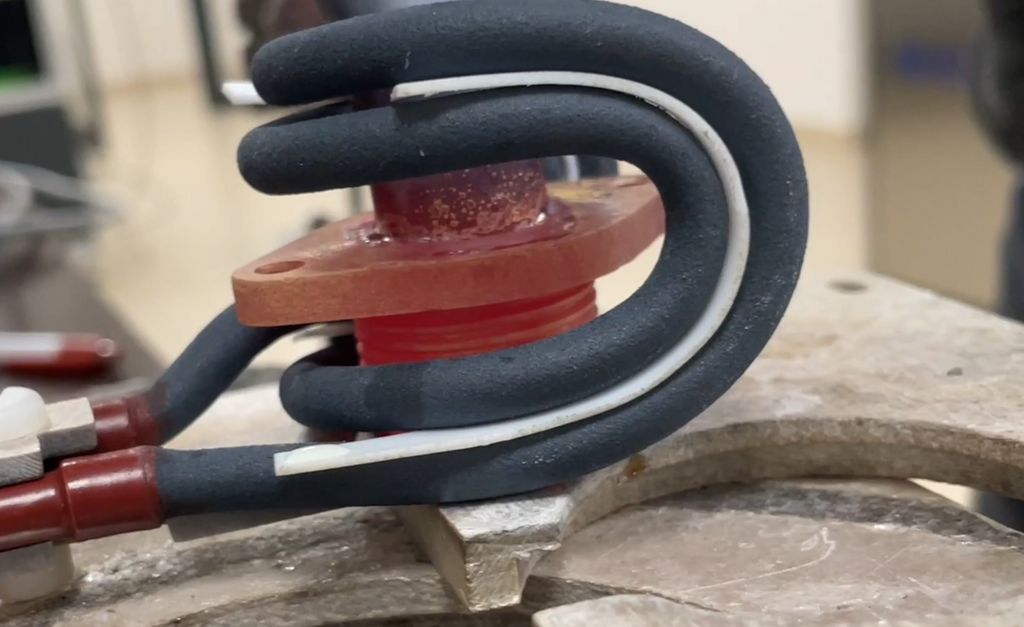
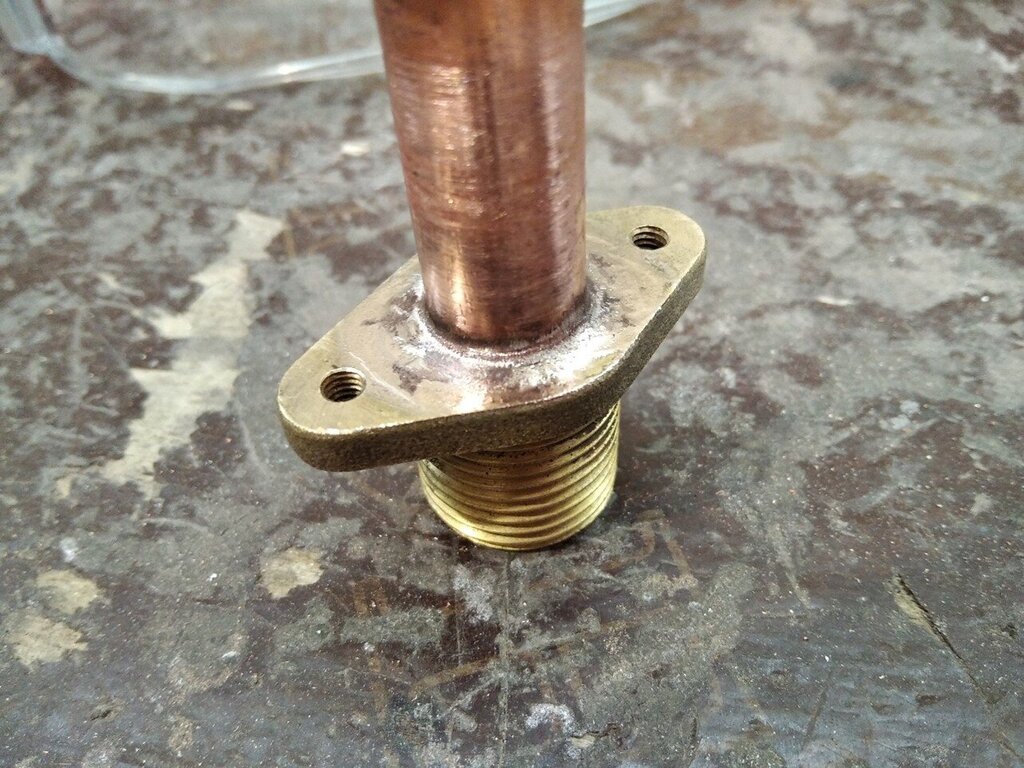


Subscribe to our YouTube Channel
Video