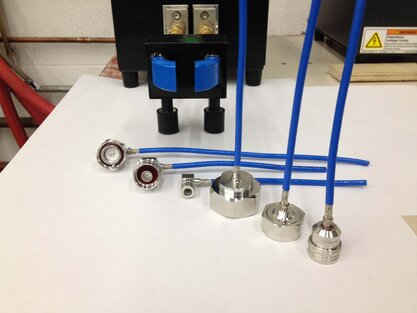
Induction Soldering Coil
Objective
Soldering coaxial cables to connectors.
Equipment
S-2 power supply, HS 4
Test Results
Key Parameters
Temperature: ~500°F (260°C)
Power: 1.3 kW
Time: 3.8-4 seconds (time varies dependent of connector and cable sizing)
Pictures
Videos
Videos
Request information or contact us about this application.